COMPRESSION STRENGTH OF THE BILLETS FROM VANADIUM-BEARING IRON POWDER WITH THE SMALL ALLOYING ADDITIVES
Polyakov P.A. 1
Dolmatov A.V. 2
Polyakov A.P. 1
1 Ural branch of Russian Academy of Sciences Institute of Engineering Science
2 Institute of Metallurgy Ural Branch RAS
In present article the strength properties of green compacts of iron-based vanadium-bearing powders with additions of Zn, Cu, P, C by tests for axial and diametral compression of cylindrical billets is made. At uni-axial compression the maximum strength received for a billet from initial powder and powder with a phosphorus additive, and the billet from the powder alloyed by graphite have a minimum strength. The results of diametral compression test showed the minimum strength for a billets with addition of phosphorus and graphite that is caused by the small resistance to a cut of a billets of this mixture. The character of damage of a billets at axial and diametral compression corresponds with the results received by other authors. Thus quantitative comparison of a damage stress value well correlates with the known literature data obtained on powders close on powder composition to research in present article. Tests on extrusion of billets at a small reduction showed that strength characteristics of billets from powder with graphite and partially from iron-phosphorus powder don’t allow to receive a solid rod.
powder composite
green compact
strength
brazilian test
extrusion
1. Akimenko V.B., Bulanov V.Ya., Gulyaev I.A., Zalazinskii G.G., Kalashnikova o.Yu., Schennikova T.L., Antsiferov V.N. Sostav, structura I svoistva zheleznykh i legirovannykh poroshkov [Composition, structure and properties of the iron and alloyed powders]. Ekaterinburg, UIF «Nauka», 1996. 351 p.
2. Akimenko V.B., Gulyaev I.A., Sekachev M.A., Kalashnikova O.Yu. Reduced Iron Powder: Manufacturing Problems and Prospects. Steel in Translation, 2011. Vol. 41. no. 7.рр. 622–626.
3. Balshin M.Yu. Nauchnye osnovy poroshkovoy metallurgii i metallurgii volokna [Scientific basis of powder metallurgy and metallurgy of fiber]. Moscow, Metallurgija, 1972, 336 p.
4. Vyal E. Yu., Laptev A.M. Strength of unsintered powder compacts with axial and radial loading. Powder Metallurgy and Metal Ceramics, 2002. Vol. 41. no. 5/6. рр. 249–252.
5. Gorokhov V.M., Prokhorov V.A., Tarusov I.N. Vliyanie temperatury pressovaniya I otnosiyel’noy plotnosti pressovok iz poroshkov diffuzionno-legirovannykh stalei na razrushayuschee napryazhenie pri razlichnykh vidakh ispytaniy [Influence of pressing temperature and relative density of powders of a diffusive-alloyed steels on a fracture stress at different types of tests] // in: Surface engineering. New powder composite materials. Welding. Part 1 / eds.: P.A. Vytiaz et al. Minsk: «Institute of powder metallurgy», 2011, рр. 92–96.
6. Metally i splavy. Spravochnik [Metals and Alloys. Reference book] / Yu.P. Solntsev (editor) St. Petersburg: Professional, 2003. 1062 p.
7. Shestakov N.A., Subich V.N., Demin V.A. Uplotnenie, konsolidatsiya I razrushenie poristykh materialov [Densification, consolidation and destruction of porous materials]. Мoscow, Fizmatlit, 2009. 269 p.
8. Doremus P. Chapter 7: Model Input Data – Failure, Series: Engineering Materials and Processes / eds. P. R. Brewin, O. Coube, P. Doremus and J.H. Tweed. Springer, 2008. рр. 95–103.
9. Gundermann Philippe. Overview of the status and trends in the European PM Industry. EURO PM 2015 REIMS. http://www.europm2015.com/post-event/plenary-presentations/103-the-european-pm-industry-current-status-and-roadmapping-the-future/file (accessed 11 November 2015).
10. Jons n P r. Fracture and Stress in Powder Compacts. Doctoral Thesis. Lule University of Technology, Lule , Sweden, 2006.
11. Proveti J.R.C., Michot G. The Brazilian test: a tool for measuring the toughness of a material and its brittle to ductile transition // International J. of Fracture, 2006. Vol. 139, no 3–4. рр. 455–460.
12. Ryabicheva L.A., Nikitin Yu.N., Beloshitskij N.V., Baranov A.G. Wastes of industry – source of raw materials for powder metallurgy // MTM’07 Conference proceedings, Bulgaria, Sofia. 2007. рр. 434–438.
13. Wittaker D. Production of Structural PM Parts // International Powder Metallurgy Directory & Yearbook. 11th Edition. 2004/2005. рр. 31–47.
Современные тенденции в области порошковой металлургии связаны с получением материалов с повышенными свойствами, малой неоднородностью свойств, высокой пластичностью. В значительной мере это относится к изделиям из порошков на основе железа. Так, в последние годы около 80 % рынка порошковых деталей в Европе приходилось на машиностроительные изделия на основе железа [9]. Поэтому фирмой H?gan?s AB (Швеция), крупнейшим европейским производителем порошков на основе железа и изделий из них, проводились исследования, в результате которых только за счет изменения состава и количества легирующих компонентов, способа их введения, применения эффективных смазок и т.п., удалось за 25 лет существенно повысить плотность и прочность деталей из таких смесей, не изменяя радикально технологию их изготовления [13]. Аналогичные работы ведутся и в России, в частности в ЦНИИЧерМет им. И.П. Бардина и других организациях [2].
Так, для повышения прочности и твердости спеченного железа в железный порошок при приготовлении порошковой смеси вводят различные легирующие добавки (фосфор, медь, хром, никель, молибден). Порошки на основе железа часто легируют углеродом, что существенно повышает их прочность после спекания [6] и т.д. Особое место занимают природно-легированные железные порошки, в которые легирующие элементы дополнительно не вводятся, а присутствуют уже в исходном сырье. Источником сырья для их получения могут, например, служить, отходы цветной металлургии – отвальные железные кеки [1]. При этом решается важная народнохозяйственная задача утилизации отходов промышленности [12].
В статье исследована прочность порошковых композиций, полученных механической активацией природно-легированных ванадийсодержащих порошков железа (состав, мас. %: 0,027 C; 0,160 Si; 0,144 Mn; 0,266 V; 0,530 O2; Fe – основа) в смеси с Zn, Cu, P, C в количестве 1,5 мас. % на измельчителе вибрационном ИВ-микро в Институте металлургии УрО РАН и имеющих следующий химический состав. Для исследований были выбраны две партии порошка железа: фракция с размером частиц < 315 мкм и фракция с размером частиц < 160 мкм. Данные о гранулометрическом составе и морфологических свойствах исходных порошков получены на анализаторе частиц по размерам и форме CAMSIZER-XT и приведены в табл. 1.
Таблица 1
Гранулометрический состав и морфологические свойства исходных порошков
Порошок
|
dср, мкм
|
SPHTср
|
Symmср
|
b/lср
|
Железо, фракция < 315 мкм
|
142
|
0,616
|
0,843
|
0,700
|
Железо, фракция < 160 мкм
|
108
|
0,571
|
0,859
|
0,712
|
Медь электролитическая
|
39,6
|
0,600
|
0,867
|
0,664
|
Цинк распыленный
|
9,5
|
0,847
|
0,887
|
0,747
|
Железо-фосфор распыленный
|
24,1
|
0,747
|
0,893
|
0,733
|
Графит карандашный
|
44,9
|
–
|
–
|
–
|
Здесь dср, мкм – медианный диаметр; SPHTср, Symmср – коэффициенты сферичности и симметричности частиц; b/lср – среднее соотношение ширины и длины частиц.
Образцы для экспериментальных исследований изготовлены на оборудовании ЦКП «Пластометрия» ИМАШ УрО РАН, на универсальной гидравлической машине Tinius Olsen Super L60. Навески порошка 9 и 1,7 г брикетировали односторонним прессованием в пресс-форме диаметром 9,6 мм при комнатной температуре и давлении 700 МПа. В результате получены цилиндрические заготовки высотой 17–18 мм (партия 1) и высотой 3,3 мм (партия 2) с относительной плотностью ?отн = 0,88–0,90. Выбор навески для 1-й партии обусловлен тем, что прессовки данных размеров предполагается использовать для экспериментальных исследований процесса выдавливания, и определяется параметрами пресс-оснастки для его реализации. Для исследований взяты по два образца каждой порошковой композиции. Поскольку плотности прессовок, полученных из композиций на основе порошка фракции < 315 мкм и фракции < 160 мкм, отличаются в пределах 1,0–1,5 %, рассмотрены усредненные значения по обеим партиям. Приняты обозначения: П1 – исходный порошок (Fe); П2 – Fe + 1,5 % Zn; П3 – Fe + 1,5 % Cu; П4 – Fe + 1,5 % P; П5 – Fe + 1,5 % C.
Выполнены исследования прочностных свойств заготовок с использованием «бразильского» теста (Brazilian test), позволяющего определить предельную поверхность условия текучести Друкера – Прагера в результате экспериментов по радиальному и осевому сжатию цилиндрических образцов. Этот способ наиболее часто используют для определения прочности хрупких материалов, в частности неспеченных порошковых заготовок [5, 11]. Также полученные результаты позволят оценить необходимость затратного по времени и энергоемкости этапа спекания в следующей схеме получения машиностроительных изделий: «порошок – прессовка – спекание – выдавливание – термообработка – деталь».
Испытания на осевое сжатие выполнены для образцов 1-й партии, на радиальное сжатие – для образцов 2-й партии. Схема проведения экспериментов показана на рис. 1.
Эксперименты выполнены на оборудовании ЦКП Урал-М в Институте металлургии УрО РАН на универсальной испытательной машине ZWICK ВТ1-АК050THW. A1K. Образцы 1-й партии испытывали с предварительной нагрузкой 5 кг до максимального усилия разрушения, скорость движения траверсы испытательной машины 2 мм/мин. Образцы 2-й партии испытывали с предварительной нагрузкой 1 кг, скорость движения траверсы 2 мм/мин.
В момент пластического разрушения заготовки – возникновения и начала роста центральной трещины фиксировали соответствующее усилие пресса и степень деформации заготовки. Для расчетов использовали формулы [8]:

где P – усилие к моменту начала разрушения образца; D, t – диаметр и толщина образца, индексы «сж» и «рад» относятся к осевому и радиальному сжатию соответственно.
По результатам испытаний выполнена оценка соответствующих пределов прочности компактного материала
по формуле М.Ю. Бальшина [3]:

где i = сж либо i = рад в зависимости от вида испытаний, m ? 3 при ?отн = 0,5–0,9.
Для качественной оценки прочности полученных брикетов приняли m = 3. Результаты испытаний образцов на осевое и радиальное сжатие представлены в табл. 2.
По результатам испытаний на осевое сжатие видим, что наибольшей прочностью обладают исходный порошок и порошок с добавкой фосфора, а наименьшей ? порошок с добавкой графита. При испытаниях на радиальное сжатие наименьшая прочность у порошков П4 и П5 (табл. 2). Рассмотрим уравнение предельной поверхности Друкера – Прагера [8]:

где ? – угол внутреннего трения; d – сопротивление срезу (сцепление); ?, ? – интенсивность касательных напряжений и среднее нормальное напряжение соответственно.
Поскольку ? = ?сж, ? = ?сж/3 при осевом сжатии и
при радиальном сжатии [8], легко убедиться, что угол внутреннего трения для исследованных порошков примерно одинаков, величина d зависит от ?рад практически линейно и характер изменения параметра d для исследованных порошковых композиций качественно повторяет результаты, полученные при испытаниях на радиальное сжатие.
Результаты экспериментов, приведенные в табл. 2, хорошо коррелируют с известными из литературы данными. Так, авторы работы [5] прессовали неспеченные образцы диаметром 25 мм и толщиной 5–10 мм из распыленного водой порошка Distaloy AЕ фирмы H?gan?s c добавками 0,6 % С и 0,6 % DN120 (пластификатор). Напряжение ?рад равно 0,35 МПа при ?отн = 0,65 и 17,5 МПа при ?отн = 0,93 (см. также [10]). Близкие к приведенным в статье результаты по прочности заготовок при осевом и радиальном сжатии получены и в работе [4] на железных порошках марки ПЖМ.
На рис. 2 показаны разрушенные образцы после испытаний на сжатие.
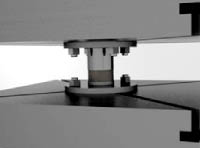
а б
Рис. 1. Схема экспериментов по «бразильскому» тесту: а – радиальное сжатие; б – осевое сжатие
Таблица 2
Результаты испытаний на осевое и радиальное сжатие
Порошок
|
Осевое сжатие
|
Радиальное сжатие
|
?отн
|
?сж, МПа
|
МПа
|
?отн
|
?рад, МПа
|
МПа
|
П1
|
0,901
|
347
|
474
|
0,897
|
25,11
|
34,79
|
П2
|
0,897
|
299
|
414
|
0,896
|
24,94
|
34,67
|
П3
|
0,891
|
314
|
443
|
0,898
|
25,97
|
35,86
|
П4
|
0,880
|
326
|
478
|
0,880
|
20,61
|
30,24
|
П5
|
0,895
|
294
|
410
|
0,895
|
20,10
|
28,03
|
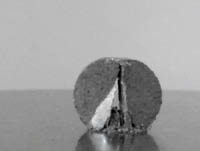
а б
Рис. 2. Разрушенные образцы: а – осевое сжатие; б – радиальное сжатие
Видим, что при осевом сжатии разрушение образца происходит от верхнего торца к нижнему по поверхности, расположенной под углом к оси приложения усилия, а при радиальном сжатии – вдоль диаметра образца по центру. Данная картина хорошо соответствует результатам, представленным в работах [8, 10].
Данные, приведенные в табл. 2, позволили также объяснить результаты эксперимента по выдавливанию неспеченных порошков П1–П5 в холодном состоянии. Выдавливали заготовки с размерами, соответствующими 1-й партии, спрессованные при давлениях 600–800 МПа при малой вытяжке (с диаметра 9,6 мм на диаметр 7,5 мм). На прутках из порошков П1-П3 наблюдаются поверхностные дефекты в виде кольцевых трещин, что соответствует известным из литературы данным [7]. На прутках из порошка железо-фосфор кольцевые трещины большего размера, на одном образце по такой трещине произошел откол. Заготовки из порошка с графитом при выдавливании полностью разрушились. Очевидно, в этом случае образовавшиеся после брикетирования межчастичные связи (сцепление) оказались недостаточно прочными и под воздействием сдвиговых деформаций при выдавливании заготовки разрушились. Таким образом, для заготовок с фосфором и особенно с графитом этап спекания перед выдавливанием является необходимым элементом технологической цепочки.
Заключение
Для неспеченных заготовок из ванадийсодержащих порошков железа с добавками Zn, Cu, P, C в количестве 1,5 мас. % выполнена оценка прочностных свойств по результатам испытаний на осевое и радиальное сжатие. Испытания на осевое сжатие показали, что наиболее прочными являются заготовки из исходного порошка и порошка железо-фосфор, наименьшей – из порошка, легированного графитом. При радиальном сжатии образцы с добавками фосфора и графита характеризуются существенно меньшими значениями разрушающей нагрузки по сравнению с остальными. Это обусловлено различием в величине предельного сопротивления срезу исследованных образцов. Эксперименты по выдавливанию заготовок при малой вытяжке показали, что прочностные характеристики порошка с графитом и частично порошка железо-фосфор не позволяют получить цельный пруток.