Влияние измельчения структуры на свойства углеродистых сталей исследовалось во многих работах [2–4]. Было отмечено, что измельчение зерна феррита при сфероидизации цементита позволяет при сохранении на высоком уровне прочности снизить температуру хрупко-вязкого перехода. Интерес к измельчению структуры углеродистых сталей существенно возрос в связи с развитием методов интенсивных пластических деформаций [1, 5]. Однако равноканальное угловое прессование, всесторонняя ковка, аккумулируемая прокатка и другие методы представляются с точки зрения технологии пока еще малоэффективными, сильно удорожающими дешевые стали. В этой связи следует обратить внимание на недавнюю работу [5]. Авторы представляют результаты экспериментальных данных, показывающие эффективность обычных прокатных технологий для получения продуктов из сталей с экстремальными свойствами. В этом же направлении выполнена работа [6]. В ней в результате измельчения микроструктуры среднеуглеродистой стали теплой прокаткой получено ультрамелкое зерно, а сталь показала экстремально высокую прочность и обратную зависимость ударной вязкости в области хрупко-вязкого перехода. Между тем по сравнению с прокаткой более эффективным видом обработки представляется ротационная ковка. Этому должны способствовать малые обжатия в ходе ковки и присутствие в схеме нагружения гидростатической компоненты напряжения. Исследования в этом направлении не проводились. В связи с этим целью настоящей работы являлось изучение эволюции структуры в ходе ротационной ковки среднеуглеродистой низколегированной стали 40ХГНМ, определение режимов формирования в ней ультрамелкозернистой структуры и оценка механических свойств.
Материал и методы исследования
В работе использовалась среднеуглеродистая низколегированная сталь марки 40ХГНМ с химическим составом, представленным в табл. 1. Пруток в исходном состоянии размерами Ø65х500 мм был подвергнут закалке при температуре 840 °С для получения структуры мартенсита. Далее заготовка была подвергнута ротационной ковке в несколько этапов. Первоначально сталь нагревали до температуры 600 °С, выдержка в печи составляла 30 минут, деформацию производили постепенно с шагом 4-6 мм на диаметр: Ø65 → Ø59 → Ø54 → Ø49 → Ø44 → Ø39 → Ø35 (режим 1). Затем заготовку разрезали на две части, одна из которых деформировалась при 600 °С, а другая − при 500 °С. Заготовки нагревали до температур 500 и 600 °С (выдержка в печи составляла 30 минут), а затем деформировали с шагом 3–5 мм на диаметр: Ø35 → Ø33 → Ø31 → Ø27 → Ø21 (режим 2.1) – и с шагом 4 мм на диаметр: Ø35 → Ø31 → Ø27 → Ø23 (режим 2.2) – соответственно. Для финального этапа сталь нагревали до температур 500 и 600оС (выдержка в печи составляла 30 минут), а затем деформировали с шагом 3 мм на диаметр: Ø21 → Ø18 → Ø15 (режим 3.1) – и с шагом 3–5 мм на диаметр: Ø23 → Ø18 → Ø15 (режим 3.2) соответственно. Охлаждение после каждого этапа ковки проводили на воздухе до комнатной температуры.
Таблица 1
Химический состав в % (вес.) стали 40ХГНМ
C |
Cr |
Mn |
Ni |
Mo |
Si |
P |
S |
0,43 |
0,63 |
0,60 |
0,72 |
0,27 |
0,41 |
0,0236 |
0,0385 |
Образцы для исследования микроструктуры вырезались в продольном и поперечном направлениях в центрах образцов. Подготовка шлифов проводилась с постепенным уменьшением зернистости наждачной бумаги. Электролитическая полировка осуществлялась на электролите А2 на установке для электролитической полировки при напряжении 27 В и комнатной температуре. Исследования микроструктуры проводились на растровом электронном микроскопе FEI Quanta-600 в режиме обратно-рассеянных электронов. Фольги для исследования тонкой структуры получали на установке TenuPol-5 на электролите состава 10 %HClO4 – 90 %CH3COOH при напряжении 33 В и комнатной температуре. Исследования тонкой структуры проводили при помощи просвечивающего электронного микроскопа JEOL при ускоряющем напряжении 200 кВ.
Образцы на растяжение вырезали в продольном направлении согласно ГОСТ 1497-84. Механические испытания проводили на установке Instron. Образцы для испытаний на ударную вязкость вырезали в продольном направлении согласно ГОСТ 9454-78, испытания проводились на маятниковом копре.
Результаты исследования и их обсуждение
Выбор в качестве исходной структуры мартенсита был обусловлен задачей получения перед деформацией наиболее тонкодисперсной и равномерной смеси карбидов. Между тем выбранная температура нагрева под закалку не привела к полному растворению исходных карбидов. В результате в мартенсите была выявлена небольшая доля карбидов размером 120 нм. Далее была проведена термомеханическая обработка путем ротационной ковки. Начальная температура нагрева заготовок под ковку была выбрана из предварительных экспериментов на осадку образцов закаленной стали. Из этих данных был определен температурный интервал ковки 600–500 °С для получения ультрамелкозернистой структуры при обеспечении достаточной технологической пластичности стали. Ввиду этого на первом этапе была выполнена деформация со степенью ~1,2 при 600 °С, а на остальных этапах деформация проводилась с нагревом на 600 °С или 500 °С.
Исследование микроструктуры прутков было выполнено после деформации со степенями ~1,2, ~2,2 и ~2,9 в поперечных и продольных сечениях (рис. 1). При деформации ~1,2 образовывались вытянутые в продольном направлении ферритные зерна, что свидетельствует о появлении текстуры, характерной для данного метода обработки (рис. 1 а,б). Дальнейшее увеличение деформации ведет к усилению текстуры при обеих температурах 500 и 600 °С (рис. 1 в, д, ж, и). В то же время при степени деформации 2,9 доля равноосных зерен в продольном сечении существенно возрастает (рис. 1 ж, и). Отметим, что снижение температуры с 600 до 500 °С ведет к увеличению неоднородности распределения деформации по поперечному сечению образца.
а) б)
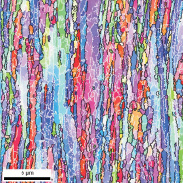
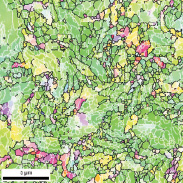
г) д)
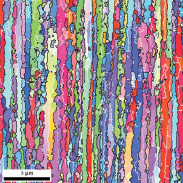
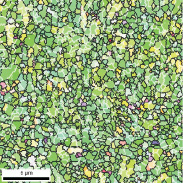
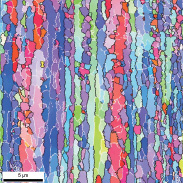
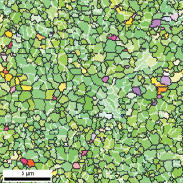
Рис. 1. Карты разориентировки границ зерен/субзерен стали 40ХГНМ после ротационной ковки: а, б – деформация ~1,2 при 600 °С; в, г – деформация ~2,2 при 500 °С;д, е – деформация ~2,2 при 600 °С; ж, з – деформация ~2,9 при 500 °С; и, к – деформация ~2,9 при 600 °С
В табл. 2 приведены параметры микроструктуры стали после различных режимов ротационной ковки по данным сканирующей микроскопии в режиме дифракции отраженных электронов. Видно, что увеличение степени деформации ведет к уменьшению размера зерна, причем наиболее заметному при снижении температуры ковки до 500 °С. В то же время средний размер зерен/субзерен даже несколько увеличивается, что отражает вклад в эту величину повышения доли большеугловых границ и связанной с ними миграцией границ.
Исследования тонкой структуры показали, что карбиды в матрице распределены равномерно, формируясь как на границах, так и в объеме зерен. Средний размер карбидов после первого этапа деформации составил 45 нм; после деформации по режиму 2.1 (ɛ~2,3) – 50 нм, 2.2 (ɛ~2,3) – 55 нм; после максимальной степени деформации при 500 °С (режим 3.1, ɛ~2,9) средний размер карбидов составляет 55 нм, при 600 °С (режим 3.2, ɛ~2,9) – 75 нм. Отчетливо наблюдаются признаки рекристаллизации: видно образование равноосных зерен, практически свободных от дислокаций (рис. 2).
Таблица 2
Параметры микроструктуры стали 40ХГНМ в поперечном сечении прутка после различных режимов ротационной ковки
Режим ротационной ковки |
dзерна, нм |
dзерна + субзерна, нм |
Доля БУГ, % |
Доля МУГ, % |
ε ~1,2; 600 °С |
705 |
410 |
52,1 |
47,9 |
ε ~2,2; 500 °С |
705 |
380 |
45,9 |
54,1 |
ε ~2,2; 600 °С |
590 |
365 |
58,3 |
41,7 |
ε ~2,9; 500 °С |
500 |
400 |
71,3 |
28,7 |
ε ~2,9; 600 °С |
580 |
460 |
74,7 |
25,3 |
Сравнительные испытания механических свойств, проведенные для образцов, подвергнутых закалке и высокому отпуску при 600 °C и кованых при 500 и 600 °C на максимальную степень деформации, показали различие в их уровне (табл. 3). Прочностные характеристики кованых при 600 °C образцов несколько снижаются по сравнению с закалкой и отпуском. Однако прочность кованых образцов при 500 °С по пределу прочности практически остается неизменной, а по пределу текучести существенно выше. Отметим также, что кованые образцы показывают заметно большую пластичность на 5–8 %, чем после закалки и высокого отпуска.
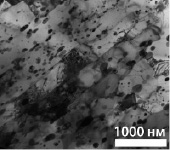
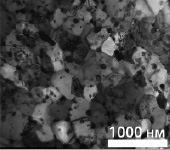
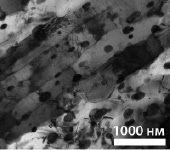
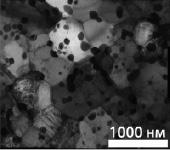
Рис. 2. Микроструктура стали 40ХГНМ после ротационной ковки на максимальную степень деформации 2,9 при 500 (а, б) и 600 °С (в, г): а, в – продольное сечение; б, г – поперечное сечение
Таблица 3
Механические свойства после испытания на растяжение в различных состояниях стали
Режимы обработки |
σ0,2, МПа |
σВ, МПа |
δ, % |
Закалка 840 °C, отпуск 600oC, 1ч. |
820 |
980 |
14 |
Закалка 840 °C, ротационная ковка 500 °С, ε~2,9 |
960 |
1000 |
19 |
Закалка 840 °C, ротационная ковка 600 °С, ε~2,9 |
830 |
900 |
22 |
Результаты испытания образцов на ударную вязкость представлены в табл. 4. Видно, что в термообработанной стали ударная вязкость непрерывно снижается с понижением температуры испытания и особенно резко уже при –20 °С. Между тем кованая сталь показывает не только повышенные значения ударной вязкости, которые более чем в четыре раза больше, чем в закаленном и отпущенном состоянии, но и повышение ее значений с понижением температуры. Интересен факт, что ударная вязкость после ковки при 500 °С и испытания при Т = –40 °С заметно снижается, но затем снова имеет рост этой характеристики. Близкая зависимость наблюдается в другом состоянии стали после ковки при Т = 600 °С, однако обнаруженный минимум наблюдается при Т = –65 °С свет ветвления трещины вдоль вытянутых ферритных зерен.
Таблица 4
Влияние режимов обработки на ударную вязкость в области хрупко-вязкого перехода
Температура испытания, °С |
+ 20 |
–20 |
–40 |
–65 |
–100 |
Ударная вязкость, Дж |
|||||
Закалка 840 °C, отпуск 600 °C, 1 ч |
52 |
30 |
26 |
22 |
17 |
Закалка 840 °C, ротационная ковка 500 °С, ε~2,9 |
235 |
278 |
202 |
280 |
291 |
Закалка 840 °C, ротационная ковка 600 °С, ε~2,9 |
223 |
258 |
270 |
217 |
261 |
Заключение
1. Интенсивная пластическая деформация методом ротационной ковки ведет к образованию вытянутых в продольном направлении ферритных зерен с размером 500 нм при 500 °С и 580 нм при 600 °С в поперечном сечении. Карбидная фаза равномерно распределена в матрице, средний размер карбидов составляет 55 нм при 500 °С и 75 нм при 600 °С.
2. Формирование ультрамелкозернистой структуры в ходе ротационной ковки приводит к увеличению пластичности стали 40ХГНМ на 5–6 % по сравнению с состоянием после закалки и высокого отпуска. Установлено, что при сравнимых температурах ковки и высокого отпуска прочностные характеристики в последнем состоянии несколько выше.
3. Формирование ультрамелкозернистой структуры в ходе ротационной ковки приводит к экстремальному росту ударной вязкости в области хрупко-вязкого перехода более чем в 4 раза по сравнению с состоянием после закалки и высокого отпуска.
Рецензенты:
Зарипов Н.Г., д.ф.-м.н., профессор, зав. кафедрой материаловедения и физики металлов ФГБОУ ВПО «Уфимский государственный технический университет», г.Уфа;
Попов А.А., д.т.н., профессор, зав. кафедрой термообработки и физики металлов Уральского федерального университета имени первого Президента России Б.Н. Ельцина Минобрнауки РФ, г. Екатеринбург.
Работа поступила в редакцию 11.01.2013.