Процессы локального деформирования (ротационная вытяжка, раскатка, ротационный обжим и другие) по сравнению с традиционными операциями обработки металлов давлением обладают рядом достоинств: меньшее деформирующее усилие, простота технологической оснастки, большие степени формоизменения заготовки.
Большая трудоемкость работ на этапе технологической подготовки производства в самолетостроении связана в известной мере с тем, что при изготовлении деталей возможности пластического деформирования исходной заготовки всегда ограничены, поэтому и в теоретическом, и в практическом плане важное значение имеют методы обработки, которые увеличивают предельные деформации заготовки. Это ведет к уменьшению технологических операций и переходов, что в конечном итоге снижает трудоемкость изготовления деталей. Поэтому исследования в области локального деформирования являются актуальными.
При раскатке (рис. 1, а) элемент трубчатой заготовки помещают между двумя роликами, которые под действием усилия Р деформируют стенку заготовки, увеличивая ее диаметр. Известна раскатка заготовок, когда взамен наружного ролика используется вращающее кольцо, или матрица (рис. 1, б) [1, 2]. В последнем случае исходная заготовка имеет первоначально меньший диаметр и раскатывается до внутреннего диаметра кольца (матрицы), что повышает точность изготовления детали.
Процессы раскатки реализуются в условиях внешнего сжатия элементов заготовки в очаге деформации, однако во внутренних слоях заготовки могут возникать и растягивающие напряжения. Из теории прокатки известно, что растягивающие напряжения в срединных слоях заготовки могут достигать значительной величины, поэтому важны такие схемы и режимы обработки, которые бы приводили к снижению этих растягивающих напряжений.
Рассмотрим симметричный процесс раскатки с двумя ведущими оправками одинакового диаметра (рис. 2). Разобьем заготовку на две равные части и в силу симметрии рассмотрим только одну (верхнюю) часть.
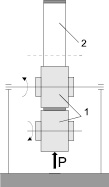
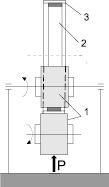
Рис. 1. Схема раскатки кольцевых заготовок: а – между двумя роликами; б – между кольцом и роликом (1 – ролики; 2 – заготовка; 3 – кольцо (матрица))
Рис. 2. К определению крутящих моментов двух ведущих оправок
Деформирование осуществляется за счет вращения оправки. Момент внешних сил М, прикладываемый к ведущей оправке, создает в зонах прилипания 2 и 3 активную силу Т23, которая обеспечивает перемещение заготовки и работу деформации, а также силы пассивного трения в зоне отставания Т1 и в зоне опережения Т4, работы которых увеличивают величину внешнего момента М.
Относительно оси вращения верхней ведущей оправки равенство моментов указанных сил имеет вид
М = (Т23 + Т1 + Т4) Rp. (1)
Для двух ведущих оправок будем иметь
2М = 2(Т23 + Т1 + Т4) Rp,
где 2Т23 Rp – внешний момент, который обеспечивает работу деформации Адеф, т.е.
2 Т23 Rp = Адеф/φ,
где φ – угол поворота оправки за один оборот заготовки.
Таким образом, выражение (1) для двух ведущих оправок может быть переписано в виде
2М = Адеф/φ + 2(Т1 + Т4) Rp . (2)
В уравнении (1) силы трения в зоне отставания Т1 и в зоне опережения Т4 равны:
(3)
где τк1, τк4 – контактные касательные напряжения от действия сил контактного трения, рассчитываемые выражениями (1), (2) соответственно; Z – единичная ширина очага деформации (Z = 1); ρ – текущий радиус.
Аналитически расчет уравнений (3) с некоторой погрешностью может быть осуществлен через средние подынтегральные значения τк1, τк4, зная размеры контактных зон.
Рассмотрим процесс раскатки с двумя оправками разного диаметра, одна из которых (верхняя) – ведущая, а вторая (нижняя) – ведомая (рис. 3).
Рис. 3. К определению крутящих моментов при одной ведущей оправке
Относительно оси вращения верхней ведущей оправки равенство моментов будет иметь вид (1), где Т23Rp – момент активной силы, необходимый для формообразования заготовки и вращения ведомой оправки, т.е.
Т23Rp = Адеф/φ + F23RР.
На ведомую (нижнюю) оправку со стороны заготовки действует активная сила F23 и силы пассивного трения F1 и F4, моменты которых уравновешиваются, т.е.
F23RQ = (F1 + F4) RQ (4)
или
F23 = (F1 + F4). (5)
Рис. 4. Схема приспособления для определения крутящего момента
Таким образом, уравнение моментов для одной ведущей оправки (рис. 3) будет иметь вид
М = Адеф/φ + F23RР + (Т1 + Т4) Rp (6)
или
М = Адеф/φ + (Т1 + Т4 + F1 + F4) Rp. (7)
Момент внешних сил (крутящий момент) определялся с использованием специального приспособления, установленного на установке для раскатки, схема которого приведена на рис. 4, а внешний вид представлен на рис. 5.
Величина момента (рис. 4) определялась по известной формуле М = Рм Н в момент перемещения заготовки под заданной нагрузкой. Влияние сил трения в передачах установки (шкив, редуктор и т.д.) компенсировалось специальной установочной гирей.
Результаты экспериментов применительно к ведущей давильной оправке Ø 24 мм и ведомой – Ø 60 мм приведены в табл. 1.
Рис. 5. Общий вид приспособления для определения крутящего момента
Таблица 1
Момент внешних сил при раскатке
№ п/п |
Заготовка, материал, размеры |
Усилие со стороны давильной оправки, кг |
Вес гирь Рм, кг |
Плечо Н, м |
Толщина в зоне контакта, мм |
Момент, М, кгм |
1 |
Полоса, АМг6М 20×1,95 мм |
500 |
3,85 |
0,34 |
1,93 |
1,29 |
2 |
750 |
3,45 |
0,34 |
1,90 |
1,17 |
|
3 |
1000 |
6,0 |
0,34 |
1,80 |
2,04 |
|
4 |
Труба Д16Т Ø 30×10×1,5 |
500 |
3,2 |
0,34 |
1,45 |
1,09 |
5 |
1000 |
4,5 |
0,34 |
1,40 |
1,53 |
|
6 |
Полоса Д16Т 20×0,95 мм |
1000 |
4,4 |
0,34 |
0,93 |
1,50 |
7 |
1500 |
6,4 |
0,34 |
0,90 |
2,18 |
|
8 |
Труба АМг6М Ø 50×24×2,1 |
1000 |
4,8 |
0,34 |
2,05 |
1,63 |
9 |
1500 |
6,5 |
0,34 |
1,95 |
2,21 |
В табл. 2 приведено сопоставление результатов расчета и эксперимента по необходимому крутящему моменту М для деформирования плоских и трубных заготовок.
Таблица 2
Результаты расчета и эксперимента по необходимому крутящему моменту М
№ п/п |
Заготовка, материал, размеры |
Погонное усилие, Р/L, кг/мм |
Длина очага, а = b, мм (экспер) |
Длина очага, а = b, мм (расчет) |
Толщина в зоне контакта, мм |
Момент, М, кгм (экспер) |
Момент, М, кгм (расчет) |
1 |
Полоса, АМг6М 20×1,95 мм |
25,0 |
1,0 |
0,6 |
1,93 |
1,29 |
1,15 |
2 |
37,5 |
1,5 |
0,9 |
1,90 |
1,17 |
2,0 |
|
3 |
50,0 |
2,0 |
1,6 |
1,80 |
2,04 |
3,4 |
|
4 |
Труба Д16Т Ø 30×10×1,5 |
50,0 |
1,0 |
0,9 |
1,45 |
1,09 |
1,9 |
5 |
100,0 |
1,8 |
1,3 |
1,40 |
1,53 |
2,7 |
|
6 |
Полоса Д16Т 20×0,95 мм |
50 |
1,0 |
0,6 |
0,93 |
1,50 |
2,4 |
7 |
75 |
1,5 |
0,9 |
0,90 |
2,18 |
3,7 |
|
8 |
Труба АМг6М Ø 50×24×2,1 |
41,7 |
1,2 |
0,94 |
2,05 |
1,63 |
2,2 |
9 |
62,5 |
1,5 |
1,33 |
1,95 |
2,21 |
3,1 |
Вывод
Из таблицы видно, что расчетные значения крутящего момента отражают физические закономерности процесса, однако превышают экспериментальные значения примерно в 1,5–2,0 раза. Это связано с приближенной зависимостью, которую (по результатам экспериментов) можно уточнить, введя в нее корректирующий коэффициент К = 0,6–0,7. С другой стороны, повышенные расчетные значения крутящего момента удовлетворяют практическим требованиям, т.к. не требуется введение так называемого коэффициента запаса по моменту (мощности) при проектировании установок для раскатки труб.
Рецензенты:
Гагарина Л.Г., д.т.н., профессор, заведующая кафедрой «Информатика и программное обеспечение вычислительных систем» Национального исследовательского университета МИЭТ, г. Москва;
Лисов О.И., д.т.н., профессор кафедры «Информатика и программное обеспечение вычислительных систем» Национального исследовательского университета МИЭТ, г. Москва.
Работа поступила в редакцию 26.08.2014.
Библиографическая ссылка
Хейн Вин Зо ТЕОРЕТИЧЕСКИЕ И ЭКСПЕРИМЕНТАЛЬНЫЕ ИССЛЕДОВАНИЯ МОМЕНТА ВНЕШНИХ СИЛ ПРИ РАСКАТКЕ ТРУБ // Фундаментальные исследования. 2014. № 9-9. С. 1959-1963;URL: https://fundamental-research.ru/ru/article/view?id=35169 (дата обращения: 04.09.2025).