DEVELOPMENT OF «IMPROVED MANAGEMENT» TO ASSESS RESOURCE TUBE FURNACE AND INCREASE THE EFFICIENCY OF EMERGENCY AUTOMATIC PROTECTION
Khafizov A.M. 1
Bashirov M.G. 1
Churagulov D.G. 1
Aslaev R.R. 1
1 Branch of SEI HPE «Ufa State Petroleum Technological University»
To increase safety exploitation tube furnaces oil and gas industry taking into account the technical state of structural elements is proposed the creation of a system of «advanced control» on the basis of the emulator processes the Honeywell UniSim Design and technical means of collection of technological and diagnostic information (sensors firms «Honeywell, Endress + Hauser, Krohne», «Yokogawa»). The program complex UniSim Design allows to model technological process, modes of operation (normal, pre-emergency, emergency) and the technical condition of the equipment, in particular the stress-strain state and the formation of deposits inside the coil tube furnace. Modeling and monitoring the areas of the coils of the tubular furnace with high stress-strain state and the level of sediments in them can prevent the occurrence and development of emergency (abnormal) situations on process plants oil and gas industry.
tube furnace
«improved management»
improvement of management systems
damage
failure
1. Bashirov M.G.. Bakhtizin R.N., Bashirova E.M., Mironova I.S. // Neftegazovoye delo: elektronnyy nauchnyy zhurnal. 2011. no. 3. рр. 26–40. URL: http://www.ogbus.ru/authors/Bashirov/Bashirov_4.pdf.
2. Vnedrenie sistem uluchshennogo upravlenija proizvodstvom Available at: http://www.infra.ru/uslugi/detail.php?ID = 65 (accessed 27 October 2015).
3. Mironova I.S., Bashirov M.G. // Fedorovskiye chteniya-2010: mater. XL Vseros. nauch.-prakt. konf. M: Izd. dom MEI. 2010. рр. 21–23.
4. Mironova I.S., BashirovM.G. // Sbornik trudov Vserossiyskoy nauchnoy konferentsii «Ekologicheskiye problemy neftedobychi» (22–25 noyabrya 2010 g.). Ufa : Neftegazovoye delo. 2010. 506 s.
5. Khafizov A.M., Bashirov M.G., Fomichev S.S., Aslay ev R.R. // Materialy dokladov X Mezhdunarodnoy molodezhnoy nauchnoy konferentsii «Tinchurinskiye chteniya» Kazan: Kazan. gos. energ. un-t. 2015. рр. 24–25.
6. Khafizov A.M., Kilsinbayev T.N., Khakimov T.I. // Materialy dokladov X Mezhdunarodnoy molodezhnoy nauchnoy konferentsii «Tinchurinskiye chteniya» Kazan: Kazan. gos. energ. un-t. 2015. рр. 11–12.
7. Khafizov A.M., Bashirov M.G. // Fedorovskiye chteniya-2014: mater. XLIV Mezhdunar. nauch.-prakt. konf. M: Izd. dom MEI. 2014. рр. 37–39.
Установки предприятий нефтегазовой отрасли являются опасными производственными объектами [4]. Анализ аварийных ситуаций на предприятиях нефтегазовой отрасли показывает, что одним из наиболее опасных объектов этой отрасли является трубчатая печь. По данным Академии государственной противопожарной службы МЧС России за 2007–2015 гг. 11,4 % аварий на объектах нефтегазовой отрасли приходится именно на трубчатые печи (рис. 1 и 3). Причинами аварий являются:
– разгерметизация змеевика – по жар в печи;
– погасание горелок – взрыв в печи;
– разгерметизация оборудования снаружи печи – взрыв снаружи печи.
Печи являются источниками образования взрывоопасных смесей. Пожары и взрывы в печах часто являются причиной разрушения оборудования, расположенного в непосредственной близости. Большинство аварий происходит из-за разгерметизации змеевика и выброса целевого продукта в объем печи. Разгерметизация змеевика происходит чаще всего из-за разрушения в зонах повышенной концентрации механических напряжений или прогара в зонах внутренних отложений. Своевременная очистка внутренней полости змеевика и предотвращение наступления предельного напряженно-деформированного состояния позволяют предупредить возникновение пожаров или взрывов.
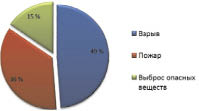
Рис. 1. Статистика аварийных ситуаций на трубчатых печах
Самым распространенным способом обеспечения промышленной и пожарной безопасности трубчатых печей является использование системы противоаварийной автоматической защиты (ПАЗ), предназначенной для предупреждения и предотвращения аварийных ситуаций, возникающих в результате действия человеческого фактора или сбоев в работе оборудования. В системах ПАЗ используются специально сертифицированные датчики, измерительные приборы, исполнительные устройства и программируемые контроллеры. Контроллеры имеют дублированную архитектуру, повышающую их надежность и, соответственно, безопасность технологических процессов. Система ПАЗ формирует управляющие воздействия на исполнительные устройства для предотвращения и развития аварийных (нештатных) ситуаций.

Рис. 2. Статистические данные о причинах аварий на предприятиях нефтегазового производства
Следует отметить, что значительная часть аварий на трубчатых печах возникает из-за неисправностей конструктивных элементов, в том числе и технических средств автоматизации, поэтому актуальным является задача оценки их технического состояния и прогнозирования ресурса безопасной эксплуатации [1, 3].
В соответствии с требованиями РД 09-102-95 «Методических указаний по определению остаточного ресурса потенциально опасных объектов, поднадзорных Госгортехнадзору России» процесс оценки технического состояния трубчатых печей состоит из следующих этапов:
– изучение технической документации печи (проектной, исполнительной, эксплуатационной);
– оперативная диагностика печи, которая проводится в период работы установки в соответствии с разработанной программой с использованием штатных контрольно-измерительных приборов установки;
– экспертное обследование печи, которое проводится в период ее остановки с целью получения информации о реальном техническом состоянии печи, ее основных элементов и узлов;
– наружный и внутренний осмотр печи и ее основных элементов. При визуальном (наружном и внутреннем) осмотре печи устанавливается состояние наружной поверхности и наличие деформаций, коррозионного и эрозионного износа и других дефектов основных элементов печи: трубного змеевика, металлоконструкций, гарнитуры, кладки и футеровки печи, боровов и газоходов, дымовых труб, горелок.
Недостатки данных методов обследования технического состояния:
– реальное техническое состояние элементов печи можно определить только в период ее остановки;
– нет возможности контролировать ухудшение технического состояния элементов трубчатой печи в режиме реального времени;
– визуальный осмотр в период работы печи не дает точно оценить все повреждения (количественно и качественно).
Проблемам обеспечения пожарной и промышленной безопасности технологических установок нефтегазового производства, содержащих трубчатые печи, посвящены работы А.А. Абросимова, П.Г. Белова, И.Р. Кузеева, Н.В. Лазарева, М.Х. Хусниярова и др. Вопросы моделирования технологических процессов нефтегазового производства для решения задач диагностики этих процессов и технологического оборудования рассматриваются в работах А.В. Мозгалевского, А.П. Веревкина, Н.Б. Кобелева, Д.С. Матвеева, Ю.Н. Федорова и др.
В данной работе рассматривается метод повышения пожарной и промышленной безопасности трубчатых печей, основанный на оптимизации системы обслуживания и ремонта оборудования. При реализации этого метода необходимо решить следующие задачи:
– моделирование технологического процесса и технического состояния элементов трубчатой печи в программном комплексе UniSim Design корпорации Honeywell;
– совершенствование системы автоматического управления трубчатой печи с использованием виртуальных анализаторов – создание системы «усовершенствованное управление» АРС (АРС – Системы усовершенствованного управления технологическими процессами [2]).
В качестве объекта исследования выбран технологический процесс гидрирования бензол-толуол-ксилольной фракции 1 и 2 ступеней, основанный на использовании трубчатой печи. Для создания компьютерной модели технологического процесса применяется программный продукт UniSim Design корпорации Honeywell. UniSim Design обеспечивает 2 режима работы: статический и динамический. В статическом режиме можно моделировать стационарный режим распределения потоков энергии и вещества. Переходные и скоротечные процессы лучше всего изучать, используя динамические модели процессов. UniSim Design содержит широкий набор инструментов, позволяющих моделировать работу различных видов технологического оборудования [5].
В данной работе разработана модель змеевика печи длиной 60 м из жаропрочной низколегированной стали 15Х5М. Поток жидкости моделируется радиально изотропным, т.е. однородным, без массовых и энергетических градиентов. Гидрогенизат с водородсодержащим газом, протекая по всей длине змеевика, равномерно нагревается за счет теплоты сгорания топливного газа, подводимого к змеевику из радиантной зоны печи.
С помощью встроенных утилит программного продукта был произведен расчет процесса образования отложений внутри змеевика трубчатой печи в зависимости от режимов работы, значений технологических параметров и длительности эксплуатации.
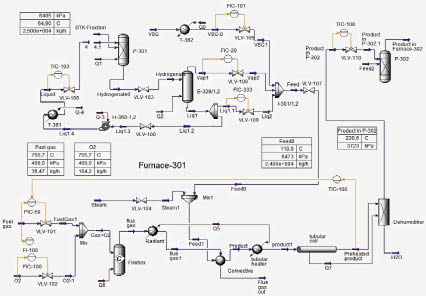
Рис. 3. Модель узла гидрирования в программном продукте UniSim Design корпорации Honeywell
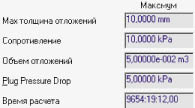
Рис. 4. Результат моделирования процесса накопления отложений в змеевике трубчатой печи
Система «усовершенствованное управление» позволяет контролировать техническое состояние технологического оборудования и управлять технологическим процессом в реальном времени. Высокая производительность системы позволяет реагировать на любые изменения технического состояния оборудования и технологического процесса, принимать необходимые решения для предотвращения возникновения и развития аварийных ситуаций. На основе компьютерной модели исследованы как режимы нормальной работы печи, так и предаварийные и аварийные режимы [6, 7].
Результаты моделирования показывают, что при параметрах технологического процесса, заданных технологическим регламентом, толщина отложений в змеевике (10 участков по 6 метров) достигает значения 1 см за 9600 часов. Аналогично можно смоделировать процесс отложения кокса на внутренней поверхности змеевика при различных значениях технологических параметров, а также и процесс формирования зон напряженно-деформированного состояния труб змеевика печи. Разработанные модели позволяют повысить эффективность технологического процесса и оборудования, оценить техническое состояние и ресурс оборудования, рассчитать оптимальное время работы печи для обеспечения надежной и безопасной эксплуатации, осуществить переход на систему обслуживания и ремонта по техническому состоянию (рис. 4). Предотвращение возникновения зон с повышенным напряженно-деформированным состоянием змеевиков печи и мониторинг толщины отложений в них позволяют существенно снизить вероятность возникновения пожаров и взрывов.