Уникальные свойства вещественного состава и строения алюмосиликатных полых микросфер, получаемых из отходов сжигания углей на тепловых электростанциях, определили широкий круг их использования в производстве керамических легковесных теплоизоляционных материалов, радиопрозрачных керамик, облегчённых тампонажных смесей и буровых растворов. [1–4]. Из микросфер можно спекать прочные агломераты, которые являются прекрасными теплоизоляторами, не уступающими по своим свойствам пенопласту. Более того, теплоизоляция из микросфер выдерживает температуры до 1000–1200 °С, в то время как пенопласт начинает плавиться при 300 °С. Испытания показали также высокую эффективность применения микросфер в химической промышленности в качестве наполнителя для различных полимерных материалов, в том числе сферопластиков и термопластиков.
За рубежом область применения полых микросфер также достаточно широка: они входят в состав стеклопластиков в комбинации со стекловолокном, заливочных паст для заделки швов (пазов, пустот), синтетических пен, высококачественных лёгких бетонов с улучшенными тепло- и звукоизоляционными характеристиками. На основе тугоплавких микросфер в США изготавливались теплозащитные керамические плитки для обшивки космических аппаратов многоразового использования. Вовлечение микросфер в сферу промышленного производства приводит к снижению стоимости продукции, увеличению её прочностных, электрических, тепловых и звукоизоляционных и других высокотехнологичных свойств, способствующих дальнейшему росту перспективных направлений утилизации СПМ и развитию минерально-сырьевой базы данного вида техногенного сырья. Если обобщить полученные данные, можно сделать вывод о том, что суммарное количество ACM, ежегодно образующихся на крупных электростанциях, составляет около 120 тыс. т. Согласно технико-экономическим расчётам, при создании установки при одной ТЭС с объёмом производства ACM в 2000 т в год экономический эффект может составить 1,5–2,5 долларов США в год в зависимости от её регионального расположения.
Авторами данной статьи впервые разработаны катализаторы на базе ценосфер для очистки дымовых газов ТЭС от NOx, SO2, CO. [5] В настоящем сообщении приведены результаты структурирования и стабилизации железо-молибденовых катализаторов окисления метанола до формальдегида в присутствии микросфер энергетических зол ТЭС.
Цель исследования – разработка и исследование наноразмерных, стабилизированных микросферическими алюмосиликатными катализаторами окисления метанола.
Результаты исследования и их обсуждение
Методически для классификации летучей золы от сжигания Экибастузского угля использовали колонный пульсационный аппарат диаметром 50 мм с пневматическими пульсаторами и завихряющими перегородками. Расстояние между перегородками составляло 80 мм, а площадь живого сечения насадки – 30 %. Скорость восходящего потока воды составляла 0,005 м/с. Амплитуду пульсации выдерживали в пределах 5 мм. Частоту пульсации варьировали в пределах отношений: плотность/ удельная поверхность, присущих двум немагнитным продуктам (кварцевый песок и g-Al2O3). В данном случае 0,2–5,0 имп./мин. В нижней части колонны расположили кольцевой электромагнит, обеспечивающий требуемый диапазон напряжённости магнитного поля в сечении восходящего потока (1000 Гс). Эффективность процесса определяли визуальным контролем за качеством выделенных продуктов с использованием электронного микроскопа. Параллельные пробы выборочно подвергали рентгенофазовому анализу. Выход полых микросфер определяли после осаждения суспензии верхнего слива колонны в отстойнике. В зависимости уровня ввода исходной суспензии выход полых микросфер составил соответственно 51, 82, 84, 88, и 89 %.
Микросферические алюмосиликатные катализаторы готовили на основе микросфер (ценосфер), выделенных из летучих зол энергетических углей. В данной работе сбор микросфер осуществляется с поверхности воды пруда-накопителя золоотвала ТЭЦ-2 (Алматы), работающей на углях Экибастузского месторождения. Фазовый состав микросфер представлен в основном кварцем и муллитом. Размеры микросфер варьируются от 150 до 250 мкм, предел прочности на сжатие 150–280 кг/см2, твёрдость по шкале Мооса – 5–6.
Типичные микроснимки выделенных алюмосиликатных микросфер представлены на рис. 1.
Химический состав (табл. 1) представлен оксидами алюминия, кремния, железа, кальция и титана (~95 масс %).
Для изучения микросферических композиций мы использовали спектральные методы. На рис. 2 представлен ИК-спектр исследуемых алюмосиликатных композитов. Наблюдается интенсивная полоса поглощения в интервале частот 1200–1000 см–1. Этот интервал частот характерен для групп Si–O, Al–O, Si–O–Al: n–1100, 1066, 1022, 1050, 900 см–1. Полосы поглощения в низкочастотной области спектра от 668 до 614 см-1 относятся к Fe–O в группе Fe2O3.
Для исследования форм и состояния железа в составе стекол (магнитоупорядоченные фазы и твердые растворы с участием катионов Fe 3 + ) успешно применяется метод ЭПР. В типичном спектре ЭПР ценосфер наблюдается узкая линия с g-фактором 4,3, а также широкая линия, являющаяся суперпозицией двух симметричных сигналов с g-факторами 2,20–2,06 (I) и 2,2–2,3 (II).
В соответствии с литературными данными сигнал в области с g = 4,3 следует приписать одиночным ионам Fe3+ , находящимся в кристаллических полях низкой симметрии и, в частности, в силикатных стеклах. Широкие сигналы I и II связаны с присутствием в ценосферах магнитоупорядоченных фаз, обуславливающих появление ферримагнетизма. Такими фазами в ценосферах могут являться кристаллические соединения со структурой шпинели в двух крайних формах: твердые растворы на основе магнетита Fe3O4, присутствие которого обнаружено в наиболее магнитных образцах методом РФА, а также феррита Mg или Mn (g = 2,2–2,10). В связи с тем, что реальный состав этих фаз, скорее всего, соответствует твердым растворам на их основе, то обозначения Fe3O4 (магнетит) и MeFe2O4 (шпинель) используются в дальнейшем достаточно условно.
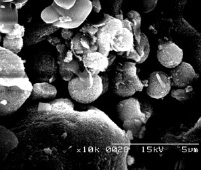
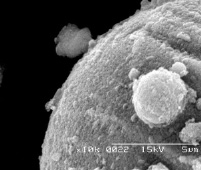
Рис. 1. Электронные микрофотографии алюмосиликатных микросфер, выделенных из золы ТЭЦ-2 г. Алматы
Таблица 1
Элементный и химический состав алюмосиликатных микросфер (ценосфер), масс. %
Образец |
Al2O3 |
SiO2 |
CaO |
TiO2 |
Fe2O3 |
Na2O |
S |
P |
SrO |
ZrO |
Исход. |
26,4 |
59,73 |
2,15 |
1,13 |
5,51 |
0,82 |
0,187 |
0,599 |
0,0407 |
0,0532 |
Рис. 2. ИК-спектр микросферических алюмосиликатов, выделенных из золы ТЭЦ-2 г. Алматы
В области малых содержаний железа (до 3–4 масс. % Fe2O3) две вышеуказанные линии (g = 2,0–2,3) являются близкими к симметричным (суперпарамагнитное состояние). С увеличением содержания железа в ценосферах появляется дополнительное поглощение в области низких магнитных полей, приводящее к анизотропии сигнала магнитного резонанса. При рассмотрении особенностей ферримагнитных фаз возможны следующие варианты:
1) размеры отдельных частиц этих фаз меньше типичных размеров доменов (монодоменное приближение);
2) размеры отдельных частиц больше размера отдельного домена, характерного для данных фаз (полидоменное приближение).
В первом случае используются различные подходы для описания спектров электронного магнитного резонанса отдельного домена. Феноменологический подход связан с описанием движения магнитного момента во внешних магнитных полях в целом. При этом в зависимости от соотношения энергий теплового движения частиц и анизотропного взаимодействия магнитного момента с внешним полем возможно усреднение анизотропии частицы (явление «суперпарамагнетизм») или появление анизотропной уширенной линии.
Данные ЭПР показывают, что железо (3+) находится в основном в двух формах: одиночные ионы Fe3+ в стекле и в частицах магнитоупорядоченной фазы шпинельной структуры размером 30–50 Å при содержании железа 3–4 масс. % Fe2O3. При содержании железа в ценосферах ниже 2 масс. % Fe2O3 железо (3+) находится преимущественно в форме одиночных ионов.
Мессбауэровские исследования ценосфер показали, что в ценосферах с содержанием более 7 масс. % Fe2O3 железо входит в состав двух фаз – дефектного магнетита (67 %) и фазы, по параметрам близкой к разупорядоченному ортосиликату монтичеллита (Ca, Mg, Fe)2SiO4 (33 %). Дефектный магнетит при комнатной температуре находится в двух магнитных равнозаселенных состояниях: ферримагнитное и суперпарамагнитное. Подрешетки магнетита разбавлены диамагнитным замещением. Диамагнитное разбавление и малый размер шпинельных образований приводит к суперпарамагнитному состоянию и разрушению быстрого электронного обмена между ионами Fe3+ и Fe2+ в В-подрешетки магнетита.
Ценосферы с меньшей концентрацией Fe2O3 (3–4 масс. %) содержат железо в составе шпинели (47 %) и ортосиликата (53 %). Шпинель находится в парамагнитном состоянии при комнатной температуре. В силикате железо в двухвалентном состоянии занимает октаэдрическую позицию типа М2.
На основе анализа результатов можно отметить следующие особенности суперпарамагнитной фазы железа по сравнению с магнетитом.
Железо смешанной валентности не обнаружено. Вероятно, быстрый электронный обмен Fe3+ ↔ Fe2+ , свойственный стехиометрическому магнетиту, разрушается совместным действием диамагнитного разбавления и дефектностью малых шпинельных областей.
Из изменения заселенностей позиций железа при уменьшении концентрации железа в ценосферах следует, что катионы Fe3+ обогащают тетраэдрическую подрешетку, вытесняя Al3+ в октаэдрическую подрешетку.
Ионы Fe3+ , обнаруженные методом ЭПР в стеклофазе в виде одиночных центров, вероятно, имеют малую заселенность и/или параметры их сверхтонкой структуры близки к параметрам Fe3+ в шпинели (рис. 3).
Рис. 3. Зависимость содержания шпинельных фаз в ценосферах по данным ЭПР
По данным термодинамических расчетов, электронного парамагнитного резонанса и Мессбауэровской спектроскопии ценосфер энергетических зол установлено, что железо входит в состав ценосфер в двух состояниях – Fe3+ и Fe2+ , при этом в области содержания железа 3–4 масс. % Fe2O3 железо (3 +) находится преимущественно в двух формах – одиночных ионов в стекле и частиц суперпарамагнитной фазы со структурой шпинели размером 30–50 Å, диспергированных в алюмосиликатном стекле. Подрешетки суперпарамагнитной шпинели диамагнитно разбавлены ионами Al3+ . Ценосферы с содержанием более 7 маcс. % Fe2O3 имеют в своем составе также магнитную фазу на основе дефектного магнетита.
Вышеприведенные результаты свидетельствуют о том, что в микросферах, выделенных из зол ТЭЦ-2, уже содержится железо, причем наноструктурированное. Пропитывание микросфер молибдатом аммония приводит к формированию железо-молибденового катализатора.
Полученные катализаторы обладают высокой механической прочностью. Элементный и химический анализ, проведённый с использованием рентгенофлуоресцентного спектрометра PhilipsPW2400 показал следующий состав (табл. 2).
Таблица 2
Элементный и химический анализ катализатора, масс. %
Наименование |
SiO2 |
Al2O3 |
Fe2O3 |
MoO3 |
Na2O |
Железо-молибденовый алюмосиликатный катализатор |
50,0–60,0 |
25,0–35,0 |
3,5–5,5 |
7,0–15,0 |
4,5–4,0 |
В ИК-спектрах алюмосиликатного катализатора наблюдаются интенсивные полосы поглощения, характерные для групп S–O, Al–O, Si–O–Al. Полосы поглощения в низкочастотной области спектра указывают на присутствие Fe3+ и W6+ в оксидах. Удельная поверхность катализаторов, вычисленная по полным изотермам низкотемпературной адсорбции азота по методу БЭТ, измеренной на приборе BelSorp (BelJapanInc.), составляет 14,7–15,8 м2/г. Интегральный объём пор катализатора, прокаленного при 400 °C, составляет 0,57 мл/г. Оптимальный размер активных частиц разработанных катализаторов – 40–50 нм.
Полученные катализаторы испытаны в процессе окисления метанола до формальдегида. Эксперимент проводили в автоматизированном универсальном проточном каталитическом реакторе – ПКУ-1. Одновременный анализ всех компонентов парогазовой смеси проводили на газохроматографическом комплексе на базе хроматографа «ХРОМОС ГХ-1000». (Разработка и производство – ООО «СOЛО» / ООО «Центр «ХромоСиб»). Результаты представлены в табл. 3–6.
Таблица 3
Влияние соотношения Mo/Fe на активность микросферического алюмосиликатного катализатора в процессе окисления метанола до формальдегида. PO2 = 13 %, удельная поверхность катализатора – 12,6 м2/г, T = 640 K. Скорость газового потока – 0,34 л/мин
Соотношение Mo/Fe |
Содержание метанола в смеси, % |
Степень превращения метанола, % |
Выход формальдегида, % |
Селективность окисления метанола в формальдегид, % |
1,1 |
6,5 |
91,8 |
90,2 |
98,3 |
1,5 |
6,5 |
93,6 |
92,85 |
99,2 |
2,0 |
6,5 |
96,2 |
96,1 |
99,9 |
2,2 |
6,5 |
97,3 |
95,15 |
97,8 |
2,5 |
6,5 |
98,4 |
93,7 |
95,2 |
Полученные результаты свидетельствуют о том, что в интервале Mo/Fe от 1,1 до 2,0 наряду с повышением степени превращения метанола, выхода формальдегида повышается и селективность окисления метанола в формальдегид.
Дальнейшее повышение соотношения Mo/Fe мало отражается на степени превращения метанола, но понижается выход формальдегида и, как следствие, селективность процесса. В продуктах реакции обнаружены: муравьиная кислота (до 3,4 %) и оксид углерода (до 1,3 %).
Повышение содержания метанола в смеси от 4,2 до 6,0 % приводит к росту практически до 100 % степени превращения метанола, выходу формальдегида и селективности процесса.
Таблица 4
Влияние содержания метанола в смеси на степень превращения метанола, выход формальдегида и селективность окисления метанола в формальдегид в присутствии микросферического алюмосиликатного катализатора. PO2 = 13 %, удельная поверхность катализатора – 12,6 м2/г, T = 640 K, скорость газового потока – 0,34 л/мин, Mo/Fe – 2,0
Содержание метанола в смеси, % |
Степень превращения метанола, % |
Выход формальдегида, % |
Селективность окисления метанола в формальдегид, % |
4,2 |
94,54 |
92,3 |
97,6 |
5,1 |
96,75 |
95,1 |
98,3 |
6,0 |
99,3 |
99,3 |
100 |
8,0 |
99,4 |
98,11 |
98,7 |
10,0 |
99,5 |
97,0 |
97,5 |
При дальнейшем повышении содержания варьируемого компонента наблюдается некоторый спад контролируемых параметров и появление небольшого количества примесей муравьиной кислоты (до 2,4 %).
Таблица 5
Влияние скорости подачи газовой смеси метанол ‒ кислород ‒ азот на степень превращения метанола, выход формальдегида и селективность окисления метанола в формальдегид в присутствии микросферического алюмосиликатного катализатора. PO2 = 13 %, удельная поверхность катализатора – 12,6 м2/г, содержание метанола в смеси – 6,0 %, кислорода – 9,0 %, T = 540 K, Mo/Fe – 2,0
Скорость газового потока, мл/мин |
Степень превращения метанола, % |
Выход формальдегида, % |
Селективность окисления метанола в формальдегид, % |
210,0 |
96,8 |
96,4 |
99,6 |
250,0 |
97,9 |
97,7 |
99,8 |
340,0 |
99,9 |
99,9 |
100,0 |
450,0 |
99,8 |
99,8 |
100,0 |
550,0 |
99,7 |
99,7 |
100,0 |
600,0 |
99,8 |
99,8 |
100,0 |
Из приведенных данных видно, что в интервале скорости газового потока CH3OH–O2–N2 от 210 до 340 мл/мин повышаются основные параметры.
Таблица 6
Влияние времени работы катализатора на его активность. PO2 = 13 %, удельная поверхность 14,7 м2/г для микросферического алюмосиликатного катализатора, T = 640 K, скорость потока CH3OH–O2–N2 – 0,34 л/мин, Mo/Fe = 2,0
Продолжительность работы катализатора, ч |
Метанол на входе, % |
Степень превращения метанола, % |
Выход формальдегида, % |
Селективность окисления метанола в формальдегид, % |
40 |
6,1 |
98,8 |
98,3 |
97,8 |
80 |
7,5 |
98,7 |
96,6 |
99,6 |
122 |
9,1 |
98,6 |
98,2 |
99,6 |
482 |
10,1 |
98,7 |
98,2 |
99,5 |
674 |
9,1 |
98,8 |
98,8 |
100,0 |
729 |
7,5 |
98,8 |
98,8 |
100,0 |
Результаты, приведенные в табл. 6, свидетельствуют о том, что силикатный катализатор во времени деградирует при повышении содержания метанола на входе до 9,0 % и возвращается к исходному значению при понижении содержания метанола до 6,12. В то же время алюмосиликатный катализатор стабилен на всем протяжении времени работы не зависимо от содержания метанола на входе.
Таким образом, полученные результаты показали, что оптимальными условиями окисления метанола в присутствии алюмосиликатного микросферического катализатора являются: соотношение Mo/Fe > 2, содержание метанола в исходной смеси CH3OH-O2-N2 – 6,0–10,0 %, кислорода – 9,0–13 %, скорость газового потока 600 мл/. В оптимальных условиях степень превращения метанола находится на уровне 99,8 % при 100 % селективности превращения его в формальдегид.
Рецензенты:
Наурызбаев М.К., д.т.н., профессор, директор ДГП на ПХВ Центр физико-химических методов исследования и анализа РГП на ПХВ, «КазНУ им. аль-Фараби» Министерства образования и науки РК, г. Алматы;
Досумов К.Д., д.х.н., профессор, заместитель директора ДГП на ПХВ Центр физико-химических методов исследования и анализа РГП на ПХВ «КазНУ им. аль-Фараби» Министерства образования и науки РК, г. Алматы.
Работа проступила в редакцию 02.06.2014.