При обработке металлов резанием режущим инструментом срезается определенный слой материала с поверхности заготовки и таким образом получается требуемая форма, размер и качество поверхности детали [3], которые являются основной целью науки резания металлов. При этом точение является одним из самых распространенных и освоенных методов изготовления деталей типа тел вращения.
Системный анализ процесса точения сборными токарными резцами показал, что при обработке режущий инструмент изнашивается, параметры сечения среза, а также направления и точки приложения вектора силы резания изменяются, жёсткость технологической системы (ТС) на разных участках обрабатываемой поверхности различна, появляются вибрация и тепловые деформации технологической системы «станок-приспособление-инструмент-деталь» (СПИД). Вследствие вышеуказанных условий ухудшается качество обработанных поверхностей [3, 11].
Шероховатость поверхности стала самым значительным техническим требованием, поскольку она является одним из самых важных показателей качества поверхностного слоя изделия. Требования к качеству выпускаемой продукции постоянно повышаются, что заставляет производителей улучшать точность и физико-механические характеристики обрабатываемых поверхностей [5]. Кроме того, качество обработанной поверхности используется в качестве важного параметра при диагностике стабильности процесса обработки, где ухудшение поверхности может указывать неоднородность материала заготовки, износ, вибрации режущего инструмента и т.п. [6]. По этим причинам важно поддерживать высокое качество обрабатываемых поверхностей, что особенно важно при современных требований при обработке изделий на наноуровне, которая должна осуществляться в пределах 100 нм. Однако достижение хорошего качества поверхности ведёт к значительным экономическим затратам при реализации производственных процессов.
Сложность и неоднозначность процесса резания металлов позволяет предположить, что возникновение шероховатости определяется рядом факторов, которые действуют одновременно. В зависимости от конкретных условий некоторые из них могут доминировать. Среди этих условий следует выделить режимы резания (скорость, подача и глубина резания), вид обработки, жесткость и демпфирующую способность элементов технологической системы, а также свойства обрабатываемого материала, которые теоретически и экспериментально исследованы во многих научно-исследовательских работах [1, 2, 7–15]. Результаты этих исследований показали, что при резании различных материалов низкая скорость резания (v), большая подача (s) и глубина резания (t), большой вылет (L), неровности режущей кромки резца, меньший размер поперечного сечения режущего инструмента и низкая жесткость технологической системы увеличивают вибрацию, вследствие чего ухудшается состояние поверхностного слоя.
При повышении требований к качеству и точности обработки стараются использовать более жесткий инструмент, который бы минимально отклонялся под действием сил резания [2]. Но такой инструмент хорошо поддерживает и сам является генератором высокочастотных колебаний, которые существенно влияют на шероховатость обработки, особенно при нанорезании. В этом случае предпочтительнее инструмент, который обладает меньшей жёсткостью, но лучшими демпфирующими характеристиками. В процессе резания его деформация (изгиб державки у резца) будет незначительна (особенно при чистовой обработке), но при этом он будет хорошо гасить колебания, и режущая кромка будет занимать стабильное положение относительно обрабатываемой поверхности. Необходимо учитывать, что из-за структурных превращений в материале заготовки, при высокой температуре (1000–1100 °С) резания, возникающей в зоне контакта резца и заготовки, изменяются механические свойства обрабатываемого материала [3]. Следовательно, конструкция режущего инструмента должна быть такой, чтобы не реагировать на уровень температуры в зоне резания.
Целью данного исследования является изучение: 1 – влияния параметров режима резания на качество обрабатываемой поверхности, и 2 – разработка конструкции сборного токарного резца, и оценка разработанной модели на качество обрабатываемой поверхности по сравнению с цельнометаллическим резцом. С этой целью для проведения экспериментов в качестве заготовки использованы три заготовки из стали, алюминия и чугуна.
Методика проведения исследований
В данном исследовании использовались стандартный сборный токарный резец и резец со сквозными горизонтальными отверстиями в державке, расположенными в шахматном порядке (Ø10 мм) со сменными многогранными пластинами (СМП) и с габаритными размерами 150×27×27 мм. Материал державок резцов – закаленная сталь 40, а материал СМП ‒ твердый сплав марки СТ35М с углом при вершине 80°, производитель Sandvik Coromant. Форма СМП: четырёхгранная с отверстием. Обрабатывались три цилиндрических заготовки, изготовленные из стали 45, алюминия Д16 и серого чугуна СЧ20 с диаметрами 68, 62 и 63 мм и с длинами 190, 160 и 175 мм соответственно. На заготовках были проточены пять канавок шириной 5 мм, разделяющие их на дорожки для удобства проведения экспериментов и измерения шероховатости. Эксперименты выполнялись на токарно-винторезном станке модели 16К20ВФ1.
При проведении экспериментов использовался метод однофакторного эксперимента, чтобы установить различные зависимости между шероховатостью и режимами резания (скорость резания, подача, глубина резания), вылетом резца и видом обрабатываемого материала. Следует отметить, что при однофакторном эксперименте каждый фактор варьируется, т.е. в каждом опыте варьируют тот фактор, влияние которого необходимо изучать, а все остальные факторы оставляются постоянными, считая, что они не зависят друг от друга и от абсолютной величины их самих [2].
Исходные данные параметров режима резания при проведении экспериментов с однофакторными зависимостями приведены в табл. 1. В табл. 1: N – частота вращения (мин–1), t – глубина резания (мм), s – подача (мм/об) и L – вылет резца (мм).
Основным показателем качества поверхности является среднее арифметическое отклонение шероховатости поверхности профиля (Ra), так как оно имеет большое влияние на эксплуатационные свойства поверхности [2]. В данном исследовании шероховатость поверхности обрабатываемых деталей измерялась профилометром модели 130 (рис. 1, б), принцип работы которого основан на сканировании алмазной иглою неровностей измеряемой поверхности в процессе её перемещения вдоль измеряемой поверхности и последующем преобразованием возникающих при этом механических колебаний иглы индуктивным датчиком в измеряемый сигнал. При сборе данных шероховатостей поверхности заготовок четыре измерения были выполнены вдоль оси заготовки под углом 90° для каждого опыта экспериментов и записаны их средние значения шероховатости.
На рис. 1, а рабочая зона станка при использовании металлического резца со сквозными горизонтальными отверстиями при: L = 50 мм; N = 400 мин–1; t = 0,05мм и s = 0,05 мм/об.
Результаты исследования и их обсуждение
После проведения экспериментов при помощи профилометра измерялись шероховатости поверхностей обрабатываемых деталей, значения которых представлены в табл. 2. На основе данных табл. 2 получены зависимости шероховатости от вида конструкции державки режущего инструмента, вида материала обрабатываемой заготовки, частоты вращения шпинделя, подачи, глубины резания и вылета резца. В качестве примера на рис. 2 построены графики зависимости шероховатости поверхности стали от частоты вращения шпинделя, подачи, глубины резания, вылета резца и от вида конструкции державки режущего инструмента.
Таблица 1
Исходные данные при однофакторном эксперименте
Факторы |
Номер эксперимента |
|||
1 |
2 |
3 |
4 |
|
Постоянные факторы |
t = 0,05 мм |
N = 1000 мин–1 |
N = 1000 мин–1 |
N = 1000 мин–1 |
s = 0,05 мм/об |
s = 0,05 мм/об |
t = 0,05 мм |
s = 0,05 мм/об |
|
L = 50 мм |
L = 50 мм |
L = 50 мм |
t = 0,05 мм |
|
Переменные факторы |
N1 = 400 мин–1 |
t1 = 0,05 мм |
s1 = 0,05 мм/об |
L1 = 41 мм |
N2 = 500 мин–1 |
t2 = 0,10 мм |
s2 = 0,06 мм/об |
L2 = 50 мм |
|
N3 = 630 мин–1 |
t3 = 0,15 мм |
s3 = 0,075 мм/об |
L3 = 65 мм |
|
N4 = 800 мин–1 |
t4 = 0,20 мм |
s4 = 0,09 мм/об |
– |
|
N5 = 1000 мин–1 |
t5 = 0,25 мм |
s5 = 0,10 мм/об |
– |
а б
Рис. 1. а – рабочая зона станка с резцом со сквозными горизонтальными отверстиями в державке при точении стали 45: 1 – шпиндель; 2 – обрабатываемая деталь; 3 – резец; 4 – резцедержатель; б – внешний вид профилометра модели 130 с управляющим компьютером при измерении шероховатости поверхности обрабатываемой заготовки
По данным табл. 2 видно, что в каждом эксперименте независимо от вида резца шероховатости поверхности алюминия и чугуна имеют наименьшее и наибольшее значения соответственно. Это объясняется хорошей обрабатываемостью алюминия и высокой зернистостью структуры чугуна при точении.
На рис. 2, а, в частности, при точении стали наглядно видно, что при постоянной глубине резания t = 0,05 мм, подаче s = 0,05 мм/об и вылете L = 50 мм с увеличением частоты вращения шпинделя значение шероховатости уменьшается. При увеличении подачи, при постоянной частоте вращения N = 1000 мин–1, глубине s = 0,05 мм/об и вылете L = 50 мм шероховатость увеличивается (рис. 2, б). Следует отметить, что такие же характеристики наблюдаются для алюминия и чугуна при изменении частоты вращения и глубины резания. Увеличение глубины резания, при постоянной частоте вращения N = 1000 мин–1, подаче s = 0,05 мм/об и вылете L = 50 мм приводит к уменьшению шероховатости поверхности (рис. 2, в). При увеличении вылета, при постоянной частоте вращения N = 1000 мин–1, подаче s = 0,05 мм/об и глубине t = 0,05 мм шероховатость уменьшается (рис. 2, г). Однако при точении алюминия и чугуна увеличение вылета ухудшает шероховатость поверхности. А при использовании резца с отверстиями в державке значение шероховатости увеличивается по сравнению с цельнометаллическим резцом. Это явление объясняется недостаточной жесткостью резца из-за отверстий в державке.
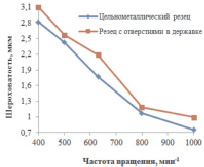
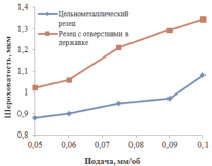
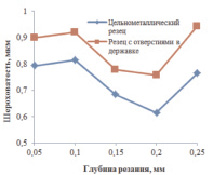
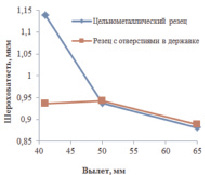
Рис. 2. Зависимость шероховатости поверхности стали от: а – частоты вращения; б – подачи; в – глубины резания; г – вылета резца
Таблица 2
Значения шероховатости поверхности обработанных деталей
Номер эксперимента |
Шероховатость (Ra), мкм |
||||||
Цельнометаллический резец |
Резец с отверстиями в державке |
||||||
Сталь |
Чугун |
Алюминий |
Сталь |
Чугун |
Алюминий |
||
1 |
N1 = 400 мин–1 |
2,81 |
2,48 |
0,942 |
3,1 |
2,65 |
1,088 |
N2 = 500 мин–1 |
2,432 |
2,13 |
0,623 |
2,57 |
2,22 |
1,046 |
|
N3 = 630 мин–1 |
1,77 |
2,06 |
0,597 |
2,186 |
2,1 |
0,977 |
|
N4 = 800 мин–1 |
1,07 |
1,918 |
0,588 |
1,181 |
2,04 |
0,929 |
|
N5 = 1000 мин–1 |
0,756 |
1,84 |
0,57 |
0,991 |
2,024 |
0,867 |
|
2 |
t1 = 0,05 мм |
0,793 |
1,717 |
0,911 |
0,899 |
1,884 |
0,924 |
t2 = 0,1 мм |
0,814 |
1,739 |
0,802 |
0,92 |
2,001 |
0,81 |
|
t3 = 0,15 мм |
0,683 |
1,725 |
0,732 |
0,777 |
1,949 |
0,734 |
|
t4 = 0,2 мм |
0,615 |
1,558 |
0,729 |
0,757 |
1,84 |
0,73 |
|
t5 = 0,25 мм |
0,764 |
1,574 |
0,696 |
0,942 |
1,782 |
0,699 |
|
3 |
S1 = 0,05 мм/об |
0,88 |
1,75 |
0,85 |
1,021 |
1,8 |
0,88 |
S2 = 0,06 мм/об |
0,9 |
1,78 |
0,88 |
1,058 |
1,88 |
0,985 |
|
S3 = 0,075 мм/об |
0,95 |
1,87 |
0,895 |
1,21 |
1,93 |
1,044 |
|
S4 = 0,09 мм/об |
0,972 |
1,9 |
0,9 |
1,295 |
1,96 |
1,064 |
|
S5 = 0,1 мм/об |
1,08 |
1,926 |
0,93 |
1,343 |
1,98 |
1,1 |
|
4 |
L1 = 41 мм |
1,139 |
1,81 |
0,791 |
0,936 |
1,744 |
0,792 |
L2 = 50 мм |
0,937 |
1,84 |
0,79 |
0,942 |
1,82 |
0,744 |
|
L3 = 65 мм |
0,881 |
1,867 |
0,835 |
0,888 |
1,989 |
0,789 |
Вывод
В данной статье экспериментально исследовано влияние разных факторов, т.е. частота вращения, глубина резания, подача, вылет и вид резца, в процессе точения деталей из разных материалов на шероховатость обрабатываемой поверхности при помощи метода однофакторного эксперимента.
После проведения экспериментов получены следующие выводы:
- При точении всех материалов (алюминий, сталь и чугун) частота вращения шпинделя и подача имеют большое влияние на шероховатость поверхности. Большая частота вращения (N = 1000 мин–1) и малая подача (s = 0,05 мм/об) улучшают шероховатость поверхности.
- При точении алюминия и чугуна увеличение глубины резания при постоянной подаче, частоте вращения и вылете улучшает шероховатость поверхности.
- Увеличение вылета резца ухудшает шероховатость обработки поверхности алюминия и чугуна и улучшает шероховатость поверхности стали. Следует отметить, что влияние вылета резца на шероховатость не очень велико.
- Обрабатываемые поверхности при использовании стандартного резца имеют лучшую шероховатость по сравнению с шероховатостью поверхностей, полученных резцом с отверстиями в державке, причиной чему является более высокая жесткость стандартного резца.
- Из трех исследованных материалов лучше всего обрабатывается алюминий и хуже всего чугун.
Резец с отверстиями в державке имеет большие технологические возможности по сравнению со стандартным. Эксперименты показали, что при больших вылетах жесткость державки недостаточна, но отверстия могут быть заполнены материалом, обладающим высокими демпфирующими характеристиками. Это позволит, с одной стороны, повысить жёсткость державки, а с другой – обеспечить гашение высокочастотных колебаний, возникающих при скоростной чистовой обработке.
После проведения эксперимента также получены режимы резания, при которых обрабатываемые детали имеют наилучшую шероховатость:
1. Для алюминия: частота вращения N = 1000 мин–1, глубина резания t = 0,05 мм, подача S = 0,05 мм/об, вылет L = 50 мм при использовании стандартного резца.
2. Для стали: частота вращения N = 1000 мин–1, глубина резания t = 0,20 мм, подача s = 0,05 мм/об, вылет L = 50 мм при использовании стандартного резца.
3. Для чугуна: частота вращения N = 1000 мин–1, глубина резания t = 0,20 мм, подача s = 0,05 мм/об, вылет L = 50 мм при использовании стандартного резца.
Рецензенты:
Расторгуев Г.А., д.т.н., профессор кафедры технологии машиностроения, металлорежущих станков и инструментов, РУДН, г. Москва;
Гусаков С.В., д.т.н., профессор, заведующий кафедрой теплотехники и тепловых двигателей инженерного факультета, РУДН, г. Москва.
Работа поступила в редакцию 16.12.2013.