Конструктивно-эксплуатационные характеристики железнодорожных колес отличает большая металлоемкость, сложность конструкции и ответственность изделия с точки зрения эксплуатационных характеристик.
Основными характеристиками, определяющими качество железнодорожного колеса, являются его надежность и срок службы. За служебные свойства изделия отвечают отдельные его элементы, в частности диск колеса, по которому чаще всего происходит усталостное разрушение. Поэтому одним из показателей, определяющих надежность колеса, является циклическая прочность в указанной зоне [2, 3]. В эксплуатации чаще всего используют колеса (рис. 1) с прямым вертикальным а, наклонным б и криволинейным в радиальном направлении диском в. Реже применяют колеса, имеющие диск с гофрами в тангенциальном направлении г.
Рис. 1. Форма дисков цельнокатаных железнодорожных колес: а – прямой вертикальный; б – наклонный, в – криволинейный в радиальном направлении;г – с гофрами в тангенциальном направлении
Другим важным показателем является износостойкость колес, зависящая от твердости и прочности металла. В настоящее время на Выксунском металлургическом комбинате (ОАО «ВМЗ») производятся грузовые колеса с твердостью обода до 360–400 HB и существует тенденция к её повышению. Для пассажирских колес более важной является безопасность эксплуатации дорожного состава. Она обеспечивается повышенными характеристиками вязкости металла при сравнительно высокой твердости обода 280–320 HB.
Развитие технологий изготовления цельных железнодорожных колес имеет длительную историю. Впервые, в начале девятнадцатого века, в силу большой металлоемкости изделия и отсутствия технологий объемной штамповки, их изготовление осуществлялось операциями свободной ковки. В двадцатом веке производство колес приобрело массовый характер, при этом, наряду с увеличением количества передвижного состава, произошло развитие параллельного транспорта, такого, как трамвай и метро. Только на ОАО «ВМЗ» в конце прошлого столетия ежегодный объем производства колес превысил половину миллиона штук. Это было обеспечено внедрением автоматизированной линии (проект ВНИИМАШ), включившей процессы формоизменения заготовки и последующей термической обработки.
Сквозные технологии изготовления цельных железнодорожных колес, независимо от страны изготовителя: Россия, США и других стран, как правило, включают следующие смежные технологии: формообразование колесной заготовки, ее термическую и механическую обработки.
Технологии формообразования колесной заготовки содержат операции горячей объемной штамповки на гидравлических прессах, которые включают операции осадки, формовки, выгибки диска, калибровку, прошивку отверстия и раскатку обода на колесопрокатном стане.
Исходной заготовкой в силу значительной массы колесной заготовки является слиток. При этом надо отметить, что перед нагревом он разделяется и используется на несколько заготовок. По истории развития, к примеру, по ОАО «ВМЗ», вначале он выплавлялся мартеновским способом и имел форму кузнечного слитка в виде «ромашки». В настоящее время, по тому же способу изготовления, он имеет цилиндрическую форму. В дальнейшем планируется переход на его производство методом непрерывной разливки стали. Спецификой действующей технологии изготовления изделия является его термомеханическая обработка, при которой формообразование заготовки выполняется в автоматизированном режиме на разноплановом кузнечно-штамповочном оборудовании за несколько операций с одного нагрева, а далее после подогрева выполняется термическая обработка, состоящая из закалки и отпуска.
Механические характеристики металла изделия определяют его служебные свойства и зависят от формируемой структуры металла в процессе его изготовления. Одним из основных факторов, влияющих на них, является степень деформации [4]. Исходя из вышесказанного, очевидна актуальность ее определения в объеме основных элементов колесной заготовки.
В настоящее время, наряду с традиционными методами оценки деформированного состояния, используется аналитический метод, основанный на методе конечных элементов (МКЭ) и проводимый с использованием специализированных программных продуктов.
Исходя из вышесказанного, была определена цель работы: оценка деформированного состояния металла в объеме изделия на основании математического моделирования технологических переходов формоизменения исходной заготовки.
Для математического моделирования процесса был выбран процесс изготовления железнодорожного колеса диаметром 957 мм согласно ТУ 0943-157-01124328-2003 из колесной стали марки Т (рис. 2).
Исходной заготовкой является часть круглого мартеновского слитка высотой 356 мм и диаметром 482 мм. Температура нагрева заготовки равнялась 1260 °С.
В соответствии с переходами формоизменения заготовки (рис. 3) были созданы трехмерные модели заготовки и технологической оснастки.
Математическое моделирование процесса проводилось с применением программного комплекса DEFORM (рис. 4).
В качестве материала заготовки для моделирования из библиотеки программного обеспечения комплекса выбрана сталь AISI-1060, которая наиболее близка по химическому составу и механическим свойствам к стали марки Т. Для оценки деформации металла в исследуемых зонах изделия (рис. 5 а) было определено их геометрическое положение по переходам формовки (рис. 5 б, в) и в исходной заготовке (рис. 5 г)), данные которых приведены в табл. 1.
Полученные результаты позволяют дать оценку расположению зон металла, из которых формируются отдельные элементы колеса в объеме исходной заготовки. По геометрии они имеют форму втулок, размеры которых приведены в табл. 2.
Рис. 2. Эскиз железнодорожного колеса и его основные элементы:1 – обод колеса; 2 – диск колеса; 3 – ступица колеса
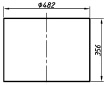
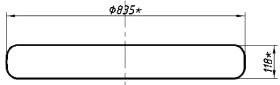
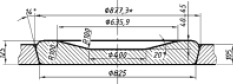
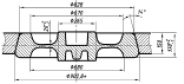
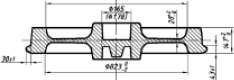
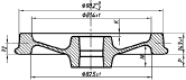
Рис. 3. Операции формообразования колесной заготовки: а – исходная заготовка; б – предварительная осадка; в − осадка и разгонка в технологическом кольце; г – формовка; д – раскатка обода; е – выгибка диска, калибровка обода, прошивка отверстия и клеймение
Таблица 1
Номер зоны i |
Координаты узлов по осям |
|||||||
Исходная заготовка |
Предварительная осадка |
Разгонка в кольце |
Формовка |
|||||
Yi |
Zi |
Yi |
Zi |
Yi |
Zi |
Yi |
Zi |
|
1 |
4760,8 |
5345,6 |
4612,9 |
5118,2 |
4580,6 |
5123,7 |
4572,5 |
5082,4 |
2 |
4759,0 |
5000,0 |
4615,1 |
5001,9 |
4584,3 |
5000,0 |
4553,6 |
4929,5 |
3 |
4862,3 |
5332,6 |
4784,2 |
5110,5 |
4735,6 |
5088,7 |
4687,7 |
5034,6 |
4 |
4849,4 |
5003,0 |
4772,3 |
5003,1 |
4721,6 |
5001,7 |
4684,7 |
4990,9 |
5 |
4888,2 |
5331,8 |
4825,9 |
5110,0 |
4783,0 |
5077,2 |
4813,8 |
5031,0 |
6 |
4887,3 |
5011,8 |
4829,3 |
5006,6 |
4782,1 |
5003,4 |
4814,7 |
4995,3 |
7 |
4926,1 |
5339,8 |
4890,1 |
5113,1 |
4859,4 |
5075,3 |
4879,4 |
5108,4 |
8 |
4934,2 |
5003,9 |
4906,9 |
5003,5 |
4875,0 |
5001,7 |
4877,0 |
4912,3 |
9 |
4958,5 |
5313,5 |
4933,7 |
5101,1 |
4908,2 |
5066,6 |
4911,5 |
5031,2 |
10 |
4968,1 |
5078,1 |
4943,8 |
5033,4 |
4917,6 |
5020,8 |
4909,7 |
4986,8 |
а) б)
в)г)
Рис. 4. Картины математического моделирования операций горячей объемной штамповки колесной заготовки: а – исходная заготовка с построенной конечно-элементной сеткой; б – предварительная осадка; в – осадка и разгонка; г – формовка
а)б)
в)г)
Рис. 5. Положения исследуемых объемов исходной заготовки по переходам формовки: а – формовка; б – осадка и разгонка; в – предварительная осадка; г – исходная заготовка
Таблица 2
Элемент железнодорожного колеса |
Размеры зон исходной заготовки, мм |
|||
в горячем состоянии |
в холодном состоянии |
|||
внешний диаметр |
внутренний диаметр |
внешний диаметр |
внутренний диаметр |
|
Обод |
483,7 |
301,2 |
482,0 |
300,0 |
Диск |
301,2 |
255,4 |
300,0 |
254,5 |
Ступица |
255,4 |
63,8 |
254,5 |
63,6 |
Перемычка под прошивку отверстия |
63,8 |
– |
63,6 |
– |
В соответствии с геометрическим положением исследуемых зон заготовки на переходах получены картины их деформированного состояния, в частности для операции формовки это показано на рис. 6. На них оценка деформированного состояния представлена показателем его интенсивности.
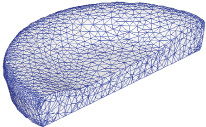
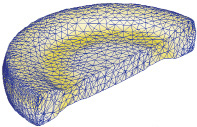
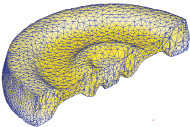
Рис. 6. Картины деформированного состояния металла на операции формовки по шагам математического моделирования: а – 100, б – 110, в – 120
Расчет итоговой деформации в исследуемых зонах изделия проводился согласно положению, по которому в условиях многопереходной объемной штамповки при немонотонном деформировании, конечное значение деформированного состояния исследуемых зон формуемого изделия можно определить арифметическим суммированием скалярных значений интенсивностей деформаций исследуемых зон на каждом из переходов [1, 5]. Значения деформированного состояния в исследуемых зонах по переходам и их итоговая деформация приведены в табл. 3.
Выводы
В процессе математического моделирования формообразующих операций изготовления заготовки железнодорожного колеса получены следующие результаты:
1. Дана оценка расположению зон металла в исходной заготовке, из которых формируются отдельные элементы колеса. Они имеют форму втулок. В частности, для наиболее ответственного элемента – диска колеса, ее внешний диаметр равен 300 мм, внутренний – 254,5 мм.
Таблица 3
Номер зоны |
Компоненты деформаций по осям и интенсивности деформаций по операциям |
Σεi |
|||||||||||
Предварительная осадка |
Разгонка в кольце |
Формовка |
|||||||||||
εr |
εθ |
εz |
εi |
εr |
εθ |
εz |
εi |
εr |
εθ |
εz |
εi |
||
1 |
0,47 |
0,64 |
–1,12 |
1,47 |
0,04 |
0,01 |
–0,09 |
0,12 |
0,00 |
0,87 |
0,50 |
0,76 |
2,34 |
2 |
0,50 |
0,56 |
–1,20 |
1,55 |
0,05 |
–0,25 |
0,16 |
0,31 |
0,06 |
0,01 |
–0,02 |
0,87 |
2,73 |
3 |
0,50 |
0,54 |
–1,04 |
1,04 |
0,13 |
0,02 |
–0,19 |
0,28 |
0,23 |
0,41 |
–0,66 |
1,17 |
2,49 |
4 |
0,47 |
0,50 |
–0,97 |
1,00 |
0,14 |
0,06 |
–0,17 |
0,22 |
0,18 |
0,07 |
–0,23 |
1,15 |
2,37 |
5 |
0,48 |
0,52 |
–1,01 |
1,01 |
0,14 |
0,10 |
–0,29 |
0,35 |
0,00 |
–0,44 |
–0,69 |
1,43 |
2,79 |
6 |
0,46 |
0,50 |
–0,99 |
0,97 |
0,16 |
0,13 |
–0,32 |
0,34 |
–0,18 |
0,63 |
–0,47 |
1,22 |
2,53 |
2. Рассчитаны итоговые значения интенсивности деформации исследуемых характерных зон изделия, а также значения на каждой формообразующей операции. Дана оценка неравномерности деформированного состояния по объему колесной заготовки и определены операции, внесшие наибольший вклад. Наибольшая итоговая деформация соответствует зонам перехода штамповки диска колеса в ступицу и перемычки для пробивки отверстия. При этом наибольший вклад в суммарную интенсивность деформации производится на стадии формовки колеса на гидравлическом прессе.
3. Полученные результаты позволяют выполнить целенаправленный анализ структурно-механических характеристик металла объема исходной заготовки и конечного изделия. В частности, для проведения дальнейшего исследования необходимо построение диаграмм рекристаллизации второго рода для колесных сталей, устанавливающих зависимость между размером зерна, интенсивностью деформации и температурой.
Рецензенты:
Гаврилов Г.Н., д.т.н., профессор кафедры «Материаловедение и технологии новых материалов» НГТУ им. Р.Е. Алексеева, г. Н. Новгород;
Филимонов В.И., д.т.н., профессор, начальник бюро Центра подготовки и переподготовки персонала и специалистов Инозаказчика ОАО «Ульяновский механический завод», г. Ульяновск.
Работа поступила в редакцию 29.10.2012.