Проведение натурных экспериментов для исследования теплоэнергетических процессов в условиях современной экономики дело крайне дорогое и порой не всегда эффективное. Этим объясняется повышенный интерес инженеров к альтернативным методам исследования, к коим относятся теоретическое и численное математическое моделирование. Последнее наиболее перспективно для использования в практической деятельности по причине большей гибкости и способности решать широкий круг задач с достаточной точностью. Это в первую очередь связано с растущими в последние десятилетия вычислительными мощностями и активным развитием универсальных программных продуктов, позволяющих с достаточной степенью точности, основываясь на численном решении подробных уравнений аэродинамики, химии и теплопереноса, исследовать различные сопряжённые явления и процессы [1]. Однако стоит признать, что совсем отказаться от физического эксперимента принципиально невозможно. Для любого класса задач необходима верификация используемой математической модели путём сопоставления расчётных данных с данными физического эксперимента. Более того, в зависимости от выбранной модели может потребоваться определение некоторых модельных параметров, которые в свою очередь возможно определить только путём проведения физического эксперимента. Дополнительными преимуществами исследований методами численного моделирования, помимо существенного сокращения денежных затрат, являются высокая скорость и широта режимных и параметрических постановок. Ограничение по времени проведения исследования определяется исключительно располагаемыми вычислительными мощностями и постановкой решаемой задачи.
В настоящее время уже накоплен некоторый положительный опыт моделирования практических важных вопросов теплоэнергетики:
- расчёт динамики потоков у горелочного устройства, подбор оптимальных параметров конструкторских решений [3];
- моделирование горения в топочных камерах: прогнозирование полей температур и тепловых потоков в зоне реакций и количества образующихся вредных веществ [7];
- исследование динамики дисперсной фазы: конструкторские решения золоуловителей [8] и процессы горения пылевидного топлива [5];
- оценка уровня шлакоотлажения на стенках топочной камеры [6];
- течения в каналах и проточных частях энергоустановок [4];
Проведение численного эксперимента особенно актуально при исследовании новых явлений и влияния каких-либо новых конструкторских решений в процессах подготовки и сжигания топлива. Так, для исследования процессов газификации пылевидного твёрдого топлива не обойтись без предварительного расчёта и поиска оптимального режима работы газификатора. В работах [9, 10] показан успешный опыт применения предварительного исследования процессов газификации угольной пыли на определённой конструкции газификатора при различных режимах его работы. Полученные расчётные значение по составу и калорийности синтез-газа с удовлетворительной точностью совпадают с результатами, полученными в ходе опытной эксплуатации установки.
В данной работе представлены результаты использования методов математического моделирования в исследовании нового способа подачи твёрдого пылевидного топлива в зону реакции газификатора, отличающегося высокой интенсивностью турбулентного смешения топлива и окислителя с одновременно относительно низкой выходной скоростью, обеспечивающей более длительное нахождение частиц топлива в зоне реакции. Способ основан на явлении автоколебательного истечения из прямоугольного отверстия, перекрытого арочным элементом [2]. Данное течение характеризуется, во-первых, аномально высокой амплитудой колебаний, во-вторых, значительным увеличением интенсивности турбулентности потока и, наконец, снижением длины результирующего течения.
Постановка задачи
Эффективность использования синтез-газа во многом зависит от его калорийности, которая в свою очередь зависит от сорта используемого угля, выбранного режима газификации и конструктивных решений по реактору газификации. Используемое пылеугольное горелочное устройство будет в значительной степени определять его теплотехнические, экологические и потребительские качества. При использовании прямоточных или вихревых горелочных устройств в газификаторах достаточно сложно обеспечить одновременно долгое нахождение угольных частиц в зоне реакции и качественное смешение реагентов, участвующих в реакциях газификации. Во многом поэтому реакторы газификаторов, работающих на пылевидном топливе, имеют достаточно большие габариты. Применение предлагаемого в данной работе способа подачи пылевоздушной смеси посредством предлагаемого горелочного устройства, обеспечивающего «гашение» выходного потока пылевоздушной смеси одновременно с значительным увеличением интенсивности турбулентности потока, может позволить уменьшить габариты реактора газификатора, что в свою очередь снизит его стоимость без потери качества производимого синтез-газа.
Стоит отметить, что данное исследование носит достаточно академический характер, преследуя цель изучить принципиальную возможность использования нового вида автоколебательного течения для приложения к данной области энергетики.
В исследовании рассматривался условный реактор газификации, (рис. 1), с габаритами 1×2×4 метра, с установленным сверху горелочным устройством, выполненным в виде простого прямоугольного отверстия, перекрытого арочным элементом (рис. 2). Размер прямоугольного выходного отверстия горелочного устройства составляет 0,1×0,2 м. Арочный элемент исполнен в полукруглой форме. Бункер подачи топлива имеет габариты 0,5×0,5×0,3 метра.
Рис. 1. Схема исследуемого реактора в продольном разрезе. Постановка граничных условий
Рис. 2. Схема горелочного устройства. Прямоугольное отверстие, перекрытое полукруглым арочным элементом
Поскольку в реакторах газификации угольной пыли в потоке стенки реактора футеруются термостойким материалом, который в свою очередь перед запуском реактора активно прогревается, то стенки рассматриваемого реактора предполагались идеально теплоизолированными. В качестве приближения диаметр угольных частиц считался постоянным и равным 90 мкм. В качестве топлива рассматривается каменный уголь штата Юта, поскольку для данного вида угля имеются экспериментально определённые параметры реакций и он по составу в наибольшей степени схож с российским каменным углём (Кузнецкий марки Д), состав которого для сравнения представлен в табл. 1. Расход угольной пыли определяется из условия режима работы газификатора, который в свою очередь определяется коэффициентом избытка воздуха. Рассматриваются режимы с коэффициентом избытка воздуха от 0,3 до 0,5. Массовая доля пара в дутье варьируется от 5 до 15 % по значению массового расхода воздуха.
Таблица 1
Сравнение состава каменных углей
Utah bit. [9] |
Кузнецкий кам. Д |
|
Влажность гигроскопическая |
6,7 |
4,5 |
Зольность |
10,4 |
18,0 |
Доля летучих |
43,5 |
40,5 |
Чистый углерод |
39,4 |
37,0 |
Элементарный состав угля, % daf |
||
C |
75,34 |
77,69 |
H |
5,29 |
5,51 |
O |
12,95 |
13,64 |
N |
1,58 |
2,62 |
S |
4,84 |
0,55 |
Теплота сгорания на сухую массу, МДж/кг |
27,4 |
21,9 |
Математическая модель
Для расчёта турбулентных течений, возникающих в исследуемом пространстве реактора газификатора, в программном комплексе STAR-CCM+ численно решается система уравнений Навье ‒ Стокса, осреднённых по Рейнольдсу (RANS), записанных в нестационарной постановке для несжимаемой жидкости. Для моделирования турбулентности используется квадратичная k-ε модель турбулентности, состоящая из двух дополнительных уравнений переноса для кинетической энергии турбулентности и скорости её диссипации. Для моделирования переноса излучения используется модель дискретных ординат (DO) с рассмотрением более 100 угловых направлений. Учитывается влияние присутствия угольной пыли в пространстве реактора на перенос теплового излучения.
Процесс сжигания и газификации пылеугольного топлива рассматривается состоящим из следующих последовательно протекающих стадий:
- Сушка и прогрев угольной пыли. На этой стадии под действием внешнего теплового потока происходит испарение остаточной гигроскопической влаги.
- Выход и сгорание летучих. На этой стадии также под действием внешнего теплового потока происходит процесс пиролиза твёрдого угля, в ходе которого образуются газообразные летучие горючие компоненты, которые, в свою очередь, при наличии окислителя воспламеняются и сгорают.
- Гетерогенные реакции горения и газификации твёрдого углистого остатка. После выхода летучих остаётся чистый углистый остаток, который трудно пиролизуется, но активно горит в твёрдой фазе и реагирует с водяным паром, образуя синтез-газ.
- Коксовый остаток. После всех стадий горения угля остаётся негорючий остаток, содержащий в основном негорючие минералы, состав которых определяется типом угля и его месторождением.
При расчёте реакций горения летучих в газовой фазе используется комбинированный подход диссипации вихрей (EDC) и конечной скорости реакции, рассчитываемой согласно закону Аррениуса. Параметры для расчёта скорости выхода летучих, скорости гетерогенных реакций горения и газификации определяются из опубликованных экспериментальных данных изучения конкретных сортов углей методами термогравиметрического анализа и микрокалориметрии [9].
Горение летучих описывается приближённой брутто-формулой
здесь формула молекул летучих определяется прежде всего из состава рассматриваемого угля. Параметры для расчёта скорости реакции, описываемой согласно закону Аррениуса, определены экспериментально [9] и равны
A = 2,119∙1011 1/c;
E = 202,7 кДж/моль.
Процесс пиролиза угольной пыли представлен в виде двух параллельно идущих реакций:
здесь k1 и k2 – скорости реакций первой и второй стадии соответственно; Y1 и Y2 – массовые стехиометрические коэффициенты. Параметры для расчёта скоростей реакций представлены в табл. 2.
Таблица 2
Параметры реакций пиролиза угля [9]
1 реакция |
2 реакция |
|
Yi |
0,1079 |
0,6384 |
Ai, 1/с |
15336,33 |
5,603∙1013 |
Ei, кДж/моль |
30,09 |
79,87 |
Процесс горения и газификации представлялся тремя параллельно идущими гетерогенными реакциями:
Для рассматриваемого сорта угля были приняты параметры реакции, представленные в табл. 2. Параметры реакций горения и газификации угля представлены в табл. 3. В данных реакциях учитывается зависимость их скорости от температуры, которая во всех случаях линейна.
Таблица 3
Параметры реакций горения и газификации угля [10]
Ea, кДж/моль |
A, 1/c |
|
|
92,9 |
2,3 |
|
147,1 |
1,33 |
|
130,1 |
3,149 |
Результаты
Для создания эффективного пылеугольного горелочного устройства использовано гидродинамическое явление автоколебательного истечения двух встречно соосных потоков. Суть явления заключается в возникновении мощного автоколебательного процесса при истечении воздуха из отверстия прямоугольной формы, перекрытого арочным элементом [2]. Форма арочного элемента может быть как полукруглой, так и прямоугольной. Основная особенность предложенного метода заключается в аномально высокой амплитуде возникающих колебаний, а также в высокой интенсивности турбулентности потока, особенно важной в процессах сжигания топлив, способствующей быстрому смешению горючих компонентов с окислителем.
Один из главных параметров, влияющих на полноту протекания реакций, это время присутствия угольных частиц в зоне реакций. Длительное присутствие в зоне реакций увеличивает вероятность полного протекания процесса газификации топлива. На рис. 3 показано различие траекторий движения частицы в реакторе при простой прямоточной подаче пылевоздушной смеси и траекторий движения с использованием предлагаемой конструкции горелочного устройства. Стоит отметить, что при использовании предлагаемой конструкции выходного отверстия время присутствия частицы в зоне реакций газификации увеличилось в 6 раз, с 0,4 до 2,5 секунд.
Сравнение распределений температуры в пространстве реактора представлено на рис. 4. Для прямоточной подачи течение развивается как струйное, а факел имеет достаточно протяжённую форму, находясь на достаточном удалении от горелочного устройства, температура при этом распределена в пространстве существенно неравномерно. Иная форма факела образуется при использовании предлагаемого устройства. Течение характеризуется более равномерным распределением температуры в пространстве реактора, а также близким расположением фронта пламени к выходному отверстию горелки.
Отметим, что при равномерном распределении частиц в реакторе создаются благоприятные условия для интенсивного протекания реакций газификации. В табл. 4 представлено сравнение составов синтез-газа, образующегося при различных режимах работы реактора, отличающихся коэффициентом избытка воздуха и массовым содержанием пара в паровоздушном дутье.
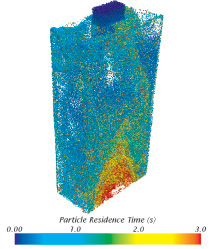
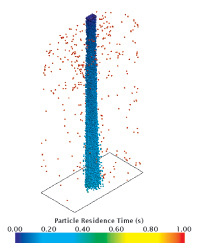
Рис. 3. Распределение угольных частиц в пространстве реактора: а – автоколебательное истечение; б – прямоточное истечение
Рис. 4. Сравнение средних полей температуры при различных способах подачи топлива: а – автоколебательное истечение; б – прямоточное истечение
Таблица 4
Состав и низшая теплота сгорания получаемого сухого синтез-газа
Состав синтез-газа |
CO, об. % |
H2, об. % |
CO2, об. % |
N2, об. % |
Теплота сгорания, МДж/м3 |
Коэффициент избытка воздуха – 0,3 |
29,87 |
12,10 |
1,20 |
56,82 |
5,084 |
Массовая доля пара в дутье – 0,05 |
|||||
Коэффициент избытка воздуха – 0,3 |
23,71 |
17,15 |
4,37 |
54,76 |
4,851 |
Массовая доля пара в дутье – 0,10 |
|||||
Коэффициент избытка воздуха – 0,3 |
21,48 |
19,96 |
5,71 |
52,85 |
4,872 |
Массовая доля пара в дутье – 0,15 |
|||||
Коэффициент избытка воздуха – 0,4 |
27,71 |
8,95 |
2,87 |
60,47 |
4,470 |
Массовая доля пара в дутье – 0,05 |
|||||
Коэффициент избытка воздуха – 0,4 |
22,40 |
13,68 |
5,13 |
58,79 |
4,310 |
Массовая доля пара в дутье – 0,10 |
|||||
Коэффициент избытка воздуха – 0,4 |
18,25 |
18,86 |
6,88 |
56,00 |
4,345 |
Массовая доля пара в дутье – 0,15 |
|||||
Коэффициент избытка воздуха – 0,5 |
24,58 |
7,81 |
4,46 |
63,15 |
3,951 |
Массовая доля пара в дутье – 0,05 |
|||||
Коэффициент избытка воздуха – 0,5 |
22,01 |
11,92 |
5,65 |
60,42 |
4,071 |
Массовая доля пара в дутье – 0,10 |
|||||
Коэффициент избытка воздуха – 0,5 |
15,32 |
18,27 |
7,33 |
57,16 |
3,910 |
Массовая доля пара в дутье – 0,15 |
Видно, что использование горелочного устройства предлагаемой конструкции позволяет эффективно газифицировать пылеугольное топливо и получать низкокалорийный синтез-газ, который в дальнейшем может использоваться в ПГУ и ГТУ. Калорийность получаемого сухого синтез-газа варьируется от 3,9 до 5,0 МДж/м3 в зависимости от режима работы реактора газификации. Видно, что оптимальный режим из многообразия рассмотренных в данной работе соответствует коэффициенту избытка воздуха 0,3 и массовой доли пара в дутье 5 %, для которого выход сухого синтез-газа составляет 2,35 нм3/кг топлива. Для сравнения укажем, что в системе газификации компании «Shell» на парокислородном дутье и при использовании каменного угля выход сухого синтез-газа составляет 2,08 нм3/кг, а в системе компании «Texaco» также для парокислородного дутья и того же вида угля выход синтез-газа составляет 2,1 нм3/кг [2]. Выгодное отличие от известных систем заключается в отсутствии необходимости организации высокого давления в реакторе: в данной работе давление в реакторе мало отличается от атмосферного, тогда как в представленных сравнительных примерах давление поддерживается выше 2,5 МПа.
Заключение
С использованием методов численного моделирования и с помощью программного комплекса STAR-CCM+ были проведены исследования динамики процессов газификации. Проведено сравнение динамики пылеугольного факела для простой прямоточной подачи пылевоздушной смеси и для новой конструкции выходного отверстия горелочного устройства. Сравнение показало:
- при использовании новой предлагаемой конструкции горелочного устройства наблюдается более равномерное распределение температуры и угольной пыли в пространстве реактора;
- время пребывания частиц в зоне реакций увеличилось в 6 раз, с 0,4 до 2,5 с;
- калорийность получаемого синтез-газа для различных режимов работы газификатора варьируется в пределах от 3,9 до 5,0 МДж/м3.
Показана принципиальная возможность подачи пылевидного топлива в реактор с использованием эффекта автоколебательного процесса при истечении из прямоугольного отверстия, перекрытого арочным элементом.
Однако остаются открытыми вопросы конструктивного исполнения и интеграции в существующие объекты энергетики исследованного решения. Отмечается достаточно близкое расположение фронта пламени к выходному отверстию горелочного устройства. Выявленные особенности предлагаемой конструкции следует учитывать в последующих разработках.
Рецензенты:
Бурцев С.И., д.т.н., профессор, управляющий партнер ЗАО «Бюро техники», г. Санкт-Петербург;
Дацюк Т.А., д.т.н., профессор, заведующая кафедрой строительной физики и химии, СПбГАСУ, г. Санкт-Петербург.
Работа поступила в редакцию 16.02.2015.
Библиографическая ссылка
Куфтырев К.А., Колосницын А.Н. ИСПОЛЬЗОВАНИЕ ЯВЛЕНИЯ АНОМАЛЬНО ВЫСОКОЙ АМПЛИТУДЫ АВТОКОЛЕБАТЕЛЬНОГО ПРОЦЕССА В ЗАДАЧАХ ПОДАЧИ ПЫЛЕВИДНОГО ТОПЛИВА В РЕАКТОР ГАЗИФИКАЦИИ // Фундаментальные исследования. 2015. № 4. С. 93-99;URL: https://fundamental-research.ru/ru/article/view?id=37129 (дата обращения: 01.09.2025).