Разработка износостойких материалов является одной из приоритетных задач современного материаловедения. Износостойкость в основном зависит от значения коэффициента трения и твердости материала. Твердость металлического материала можно увеличить различными способами обработки [2, 3, 4] или изготавливать материал, обладающий гетерогенной структурой с твердым наполнителем. Частицы наполнителя выступают в качестве несущих включений, снижают склонность к схватыванию, обладают высокой твердостью, а также в ряде случаев имеют более низкий коэффициент трения по сравнению с матрицей [5, 6, 7].
Методы порошковой металлургии позволяют получать функциональные, износостойкие, гетерогенные, ресурсосберегающие материалы с заданными свойствами, способные удовлетворять возрастающим требованиям, которые предъявляются к деталям машин [1, 6, 7].
Представляют интерес порошковые металлостеклянные материалы, полученные холодным прессованием шихты и спеканием. Такие материалы способны работать в условиях отсутствия смазки и вакууме, обладают высокими физико-механическими и антифрикционными свойствами, имеют низкую стоимость по сравнению с инструментальными легированными сталями [5, 6].
В настоящей работе исследованы структура и свойства материалов на основе порошка восстановленного карбонильного железа с добавками графита и порошка тарного стекла. Показано влияние твердого наполнителя на прочность и микротвердость металлостеклянного материала.
Материалы и методы исследований
Для исследования влияния твердого наполнителя и его количества на прочность и микротвердость материала был проведен полный факторный эксперимент по плану 22. При разработке матрицы планирования эксперимента были поставлены следующие задачи: изучение процесса структурообразования при различном содержании углерода и закономерности изменения механических свойств в зависимости от количества стеклянного наполнителя с размерами частиц менее 63 мкм. В табл. 1 представлены уровни факторов и интервалы их изменения при исследовании металлостеклянного материала.
Основа исходной шихты – порошок восстановленного карбонильного железа марки ВК-1 ТУ 2436-005-74439740-14. Гранулометрический и химический состав порошка представлен в табл. 2. Содержание углерода обеспечивалось введением в шихту графита карандашного марки ГК-1 ГОСТ 4404-78. Порошок стекла получали размолом стеклобоя в шаровой мельнице в течение 10 часов. От полученного порошка были отсеяны частицы размером менее 63 мкм. Порошки железа и графита также подвергались отсеву через сито с размерами ячейки 63 мкм.
Содержание углерода в шихте было выбрано таким образом, чтобы охватить диапазон широко используемых машиностроительных сталей от углеродистой конструкционной стали 40 до углеродистой инструментальной стали У7. Содержание стекла выбиралось из расчета его объемного содержания в материале от 7 до 32 об. %. Объемное содержание переведено в массовое, исходя из плотности компонентов (плотность стекла – 2500 кг/м3). Матрица планирования эксперимента, предел прочности при растяжении и микротвердость приведены в табл. 3.
Таблица 1
Уровни факторов при исследовании металлостеклянных материалов
Исходные данные |
Кодированное значение факторов xi |
Натуральные значения факторов |
|
Содержание углерода, % |
Содержание стекла, % |
||
x1 Нат. |
x2 Нат. |
||
Основной уровень xi 0 |
0 |
0,55 |
7,75 |
Интервал изменения Δxi |
– |
0,15 |
5,5 |
Верхний уровень xi 0 + Δxi |
+ 1 |
0,7 |
13,25 |
Нижний уровень xi 0 – Δxi |
–1 |
0,4 |
2,25 |
Таблица 2
Гранулометрический и химический состав порошка ВК-1
Гранулометрический состав, мкм, не более |
Массовая доля химических элементов, не более |
||||||
Х10 |
Х50 |
Х90 |
Fe, % |
C, % |
N, % |
O, % |
S, % |
4 |
8 |
18 |
основа |
0,02–0,1 |
0,02 |
0,3 |
0,005 |
Таблица 3
Матрица планирования эксперимента и результаты измерений
Номер опыта i |
Значения факторов |
Параметры оптимизации |
||||
x1 |
x2 |
y1 |
y2 |
|||
код. |
нат., % |
код. |
нат., % |
σВ, МПа |
HV, МПа |
|
Опыты на верхнем и нижнем уровне |
||||||
1 |
+ 1 |
0,7 |
+ 1 |
13,25 |
99 |
1330 |
2 |
–1 |
0,4 |
+ 1 |
13,25 |
101 |
1326 |
3 |
+ 1 |
0,7 |
–1 |
2,25 |
190 |
984 |
4 |
–1 |
0,4 |
–1 |
2,25 |
208 |
1093 |
Параллельные опыты на основном уровне |
||||||
5–1 |
0 |
0,55 |
0 |
7,75 |
135 |
1122 |
6–2 |
0 |
0,55 |
0 |
7,75 |
121 |
1149 |
7–3 |
0 |
0,55 |
0 |
7,75 |
137 |
1167 |
Таблица 4
Плотность и пористость после спекания
Номер опыта |
Теоретическая плотность, г/см3 |
Плотность после прессования и спекания, г/см3 |
Пористость, % |
Процент от теоретической плотности |
1 |
6,041 |
5,02 |
17,0 |
0,830 |
2 |
6,078 |
5,19 |
14,7 |
0,853 |
3 |
7,380 |
6,24 |
15,5 |
0,845 |
4 |
7,436 |
6,34 |
14,7 |
0,853 |
5–7 |
6,666 |
5,67 |
15,0 |
0,850 |
Таблица 5
Твердость HRB (980,7 Н (100 кгс); шарик диаметром 1/16’)
Номер опыта |
|
|
Sx |
KB |
±μ |
ε, % |
Nmin |
1 |
30 |
49 |
7 |
23,4 |
4,057 |
13,5 |
10 |
2 |
29,1 |
59,9 |
7,7 |
26,6 |
4,486 |
15,4 |
10 |
3 |
22,2 |
23,1 |
4,8 |
21,7 |
2,788 |
12,6 |
10 |
4 |
17,6 |
10 |
3,2 |
18 |
1,83 |
10,4 |
10 |
5-7 |
35,1 |
16,7 |
4,1 |
11,6 |
1,269 |
3,6 |
30 |
Шихта смешивалась в лабораторном баночном смесителе в течение 240 минут и подвергалась одностороннему прессованию в закрытой пресс-форме при давлении 600 МПа. Полученные прессовки имеют размеры 2,5×4,0×60,0 мм.
Спекание проводили в вакууме порядка 5·10–5 мм рт.ст. в течение 120 минут при температуре 1100 °С. После спекания определяли плотность и расчетное значение пористости прессовок (табл. 4). Образцы испытывали на статическое растяжение с помощью универсальной машины Inspekt 50 kN при скорости приложения нагрузки 1,0 мм/мин. Форма и размер образцов на растяжение соответствует спеченным прессовкам, дополнительное изменение формы прессовок не производилось. Значение предела прочности определяли по 10-ти образцам для каждого опыта в матрице планирования эксперимента. Микротвердость измеряли на микротвердомере ПМТ-3 (нагрузка – 1,96 Н). Значение микротвердости определяли по результатам 30-ти измерений для каждого опыта в матрице планирования эксперимента. Фотографии микроструктур полученных металлостеклянных материалов представлены на рис. 3.
Дополнительно, после спекания прессовок, измерялась твердость HRB на твердомере ТК-2 «Роквелл». Среднее значение твердости HRB определяли по 10-ти измерениям для каждого опыта в матрице планирования эксперимента (табл. 5).
Результаты исследований и их обсуждение
По полученным данным (табл. 3) производились вычисления с целью получения уравнений регрессии первого порядка для описания изменения предела прочности при растяжении и микротвердости металлостеклянного материала, в зависимости от содержания углерода и порошка стекла. В результате проверки статистической значимости расчетных коэффициентов эксперимент выродился в однофакторный, и были получены следующие уравнения (1), (2).
По параметру «Предел прочности при растяжении, МПа»:
y1 = 131 – 50х2, (1)
где y1 – расчетное значение предела прочности при растяжении, МПа; х2 – содержание порошка стекла, в кодовом масштабе.
По параметру «Микротвердость HV200, МПа»:
y2 = 1146 + 145х2, (2)
где y2 – расчетное значение микротвердости HV200, МПа; х2 – содержание порошка стекла, в кодовом масштабе.
В представленных уравнениях факторы имеют кодовый масштаб. Поскольку статистически значимым оказался только фактор х2 – «Содержание стекла, %», формула перехода от кодированных величин к натуральным приводится только для него:
(3)
где х2 – содержание порошка стекла в кодовом масштабе; Х2 – содержание порошка стекла в натуральном масштабе, %; x2 Нат.0 – содержание порошка стекла в натуральном масштабе на основном уровне, %; Δx2 – интервал изменения содержания порошка стекла в натуральном масштабе, %.
Проверка полученных уравнений на адекватность по критерию Фишера при уровне значимости α = 0,05 показала, что гипотеза об адекватности полученных уравнений регрессии не отвергается. Расчетные и табличные значения критерия Фишера приведены в табл. 6.
Таблица 6
Значения расчетного и табличного критерия Фишера.
Уравнение |
Fрасч |
Fтабл |
Условие – Fрасч < Fтабл |
y1 = 131 – 50х2 |
10,10 |
19,0 |
выполняется |
y2 = 1146 + 145х2 |
11,21 |
19,0 |
выполняется |
Рис. 1. Экспериментальные значения и расчетная зависимость предела прочности при растяжении от содержания порошка стекла
Рис. 2. Экспериментальные значения и расчетная зависимость микротвердости от содержания порошка стекла
Сопоставление расчетных значений предела прочности при растяжении и микротвердости с экспериментальными данными графически представлено на рис. 1 и 2.
Структура металлической матрицы полученных материалов состоит из феррита и незначительного количества перлитных колоний, которые имеют тонкопластинчатое и сорбитообразное строение. Частиц свободного графита в микроструктуре не выявлено. Очевидно, это связано с частичным выгоранием графита из материала в процессе спекания. Аналогичное явление (при спекании в водороде порошковых композиций железо-графит) было установлено в работе [7]. Соответственно, углерода в железе растворилось недостаточно и значительного эффекта упрочнения от этого фактора не получено. Это объясняет статистическую незначимость коэффициента, отражающего влияние углерода.
Недостаточное содержание углерода в металлической матрице материала косвенно подтверждается низкой твердостью HRB (табл. 5). Однако значения твердости HRB имеют большую относительную ошибку, что связано с неравномерностью структуры материала и наличием пор.
а
г

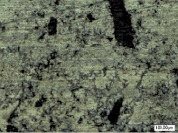
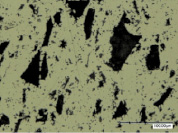
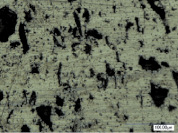
Рис. 3. Микроструктура композита, х1000 (реактив для травления – 4 % раствор HNO3 в этиловом спирте): а – микроструктура материала (Опыт № 1, 2), до травления; б – микроструктура материала (Опыт № 3, 4), до травления; в – микроструктура материала (Опыты № 5–7), до травления; г – микроструктура материала (Опыт № 1, 2), после травления; д – микроструктура материала (Опыт № 3, 4), после травления; ж – микроструктура материала (Опыты № 5–7), после травления
Частицы стекла на фотографиях микроструктуры незначительно оплавлены и окружены переходной зоной, состоящей из ортосиликата железа (II) Fe2SiO4 – файялита, образовавшегося при ситаллизации в процессе спекания. Включения стекла имеют размер от 100 мкм и менее. Очевидно, при спекании произошла коагуляция частиц стекла, имевших общую границу раздела [5, 6].
В микроструктуре присутствуют поры, однако значения пористости после спекания прессовок на 10–13 % меньше, чем в [7]. Снижение пористости в указанных пределах объясняется применением высокодисперсного порошка восстановленного карбонильного железа.
Содержание порошка стекла в полученных материалах, судя по коэффициентам в уравнениях регрессии (1, 2), значительно влияет на показатели прочности и микротвердости.
Наличие стеклянного наполнителя снижает прочность материала пропорционально его содержанию, что связано с уменьшением площади металлических связей, а также с угловатой формой частиц порошка стекла, которая способствует образованию большого количества концентраторов напряжений.
В связи с этим для повышения прочности материала необходимо использовать порошок стекла более благоприятной формы (сферической или полигональной), а также увеличить его дисперсность.
Значения предела прочности на растяжение полученных металлостеклянных материалов хорошо согласуются с известными данными для спеченного пористого железа. Так, предел прочности спеченного пористого железа составляет 98–216 МПа при плотности 5,1–6,6 г/см3 [6].
Микротвердость исследованных металлостеклянных материалов, напротив, повышается с ростом содержания порошка стекла, так как частицы стекла выступают как твердые несущие включения. Повышение микротвердости положительно влияет на износостойкость материала.
Выводы
1. Исследованные металлостеклянные композиции на основе порошка восстановленного карбонильного железа обладают всеми необходимыми свойствами, характерными для антифрикционных материалов.
2. Содержание порошка стекла с размером частиц менее 63 мкм в концентрациях от 2,25 до 13,25 масс. % приводит к линейному снижению предела прочности более чем на 35 %.
3. Стеклянный наполнитель линейно повышает микротвердость материала до 25 % с увеличением концентрации порошка стекла от 2,25 до 13,25 масс. %.
4. При спекании материалов, содержащих в шихте графит в качестве источника углерода, необходимо принимать меры по устранению его выгорания в процессе спекания, что позволит увеличить прочность металлической матрицы и материала в целом.
Рецензенты:
Дорофеев В.Ю., д.т.н., профессор кафедры «Материаловедение и технология материалов», Южно-Российский государственный политехнический университет имени М.И. Платова, г. Новочеркасск;
Васильев В.А., д.т.н., профессор кафедры «Металлургические технологии и оборудование», Нижегородский государственный технический университет им. Р.Е. Алексеева, г. Нижний Новгород.
Работа поступила в редакцию 15.02.2015.
Библиографическая ссылка
Беляев Е.С., Колосова Т.М., Алексеев В.А., Макаров Н.В., Гетмановский Ю.А. СТРУКТУРА И СВОЙСТВА МЕТАЛЛОСТЕКЛЯННЫХ МАТЕРИАЛОВ НА ОСНОВЕ ПОРОШКА КАРБОНИЛЬНОГО ЖЕЛЕЗА // Фундаментальные исследования. 2015. № 4. С. 22-27;URL: https://fundamental-research.ru/ru/article/view?id=37117 (дата обращения: 07.09.2025).