На сегодняшний день эффективность работы машин и механизмов во всех сферах деятельности человека зависит от качества используемых смазочных материалов. Наиболее простым и экономически выгодным способом улучшения качества смазочных материалов является использование в их составе различных антифрикционных и противоизносных добавок. В настоящее время для этого широко используют дисульфид молибдена и графит [1]. Однако использование графита ограничено его относительно низкими трибологическими характеристиками, а дисульфид молибдена имеет высокую стоимость. Кроме того, в ходе эксплуатации MoS2 постепенно разлагается с образованием коррозионно активной серной кислоты и оксидов молибдена, имеющих высокое абразивное действие [2].
В последние годы большое внимание было уделено поиску новых высокоэффективных антифрикционных добавок, имеющих, так же как и графит и дисульфид молибдена, слоистую структуру. Кроме того, было обнаружено, что при использовании наноразмерных порошков антифрикционных добавок (наноразмерные дисульфид и трисульфид молибдена, дисульфид вольфрама, диселениды молибдена, вольфрама и ниобия, нитрид бора, иодиды кадмия, свинца и висмута, закись меди, фторид кальция, а также ряд полимеров, природных и синтетических серпентинитов) трибологические характеристики смазочных материалов превосходят результаты, полученные с использованием порошков микроразмерного фракционного состава [3–6]. Однако высокая стоимость перечисленных нанопорошков ограничивает их внедрение в производство.
Между тем известен целый класс относительно дешевых соединений, наноразмерные частицы которых также имеют слоистую структуру – слоистые двойные гидроксиды (СДГ), однако трибологические своства представителей этого класса соединений до сих пор исследовались группой китайских авторов в очень узком диапазоне составов, в частности в системах Co–Al–CO3, Mg–Al–CO3, Ni–Al–NO3 [7–9]. Полученные результаты показали существенное улучшение трибологических характеристик смазочных композиций, однако выбор системы СДГ в проведенных исследованиях носил случайный характер.
Следует отметить, что в общем случае слоистые двойные гидроксиды представляют собой соединения состава M2+1-xM3+x(OH)2[(Аn–)x/n∙mH2O], где Аn– является анионом. На сегодняшний день известны СДГ, содержащие M2+ = Mg, Zn, Fe, Co, Ni, Cu, Cd, Sn, Mn, Pd, Pt; M3+ = Al, Fe, Cr, Mn, Ga, In, Bi, Y, La, V, Rh, Ir, Ru, и в которых в качестве аниона- могут выступают (CO32–, OH-, NO3–, SO42–, ClO4–, Cl– [10].
В зависимости от условий синтеза и состава слоистого двойного гидроксида могут образовываться различные структурные типы СДГ. При этом анионы располагаются в межслоевом пространстве таким образом, чтобы минимизировать его размер. Однако с увеличением отношения M3+/M2+ увеличивается положительный заряд слоев гидроксидов металла и для компенсации необходимо большее количество анионов. В том случае, если заряд анионов низкий, то они могут не входить в межслоевое пространство из-за геометрических соображений. К примеру, в соединении Mg0,79Al0,21(OH)2[{NO3}0,21∙0,4H2O] нитрат-ионы располагаются параллельно гидроксидным слоям.
Основным методом синтеза слоистых двойных гидроксидов является соосаждение из растворов солей M2+ и M3+ щелочью при контролируемом значении pH [11].
(1 – x)M2+ + xM3+ + 2OH- + (x/n)Аn– → M2+1-xM3+x(OH)2[(Аn–)x/n].
При этом необходимо учитывать, что способность различных анионов к интеркаляции в межслоевое пространство существенно отличается, и в присутствии в растворе двух и более различных анионов может происходить внедрение только одного из них [12]. Интервал pH, в котором проводится синтез СДГ, подбирается, как правило, экспериментально для каждой конкретной системы [13].
С учетом механизма взаимодействия антифрикционных добавок с поверхностью металла пары трения, при правильном выборе химического состава синтезируемого СДГ можно одновременно добиться увеличения износостойкости трущихся поверхностей и снижения величины коэффициента трения.
Известно, что Cr оказывает положительное влияние на износостойкость стали, в то же время добавки Zn способствовуют снижению коэффициента трения (плакирующая добавка) [14]. Исходя из вышесказанного, в настоящей работе были синтезированы слоистые двойные гидроксиды системы Zn(1-x)Crx(OH)2[(NO3))x/n∙mH2O. Нитратная форма СДГ была выбрана в связи с низкой склонностью NO3– к интераляции в межслойное пространство частиц СДГ для снижения содержания коррозионноактивного кислотного остатка в составе антифрикционной добавки [12], а величина (х) варьировалась с целью выяснения влияния соотношения компонентов на трибологические свойства синтезированного соединения.
Материалы и методы исследования
При синтезе СДГ навески двух солей соответствующих металлов марки х.ч., взятых в определенных стехиометрических соотношениях [Zn(NO3)2∙6H2O]/[Cr(NO3)3∙9H2O], а именно (в моль/л): 0,75:0,25, 0,66:0,33 и 0,5:0,5, переносили в мерную колбу на 100 мл, доводили объем до метки дистиллированной водой и перемешивали до полного растворения. Во всех вариантах общая концентрация солей в рабочем растворе составляла 1 моль/л. Соосаждение СДГ проводили 3 М раствором KOH (марки х.ч.) с использованием капельницы при постоянной скорости введения щелочного раствора (2,5 мл/мин), поддерживая при этом постоянное значение рН среды на уровне 10,00 ± 0,15. Контроль величины рН проводили с помощью стеклянного электрода марки ЭСК-10303/7 и рН-метра марки 150 М.
Полученный осадки оставляли в маточном растворе при постоянном перемешивании на магнитной мешалке в течение 2 часов с последующем выдерживанием без перемешивания в течение 48 часов для формирования слоистой структуры СДГ. Далее осадок отделяли декантацией и заливали дистиллированной водой. Данную процедуру повторяли до установления постоянного значения pH. Далее образцы помещались в сушильный шкаф, высушивались в течение 48 часов при температуре 60 °С и перетирали в агатовой ступке до порошкообразного состояния.
Морфологию частиц синтезированных СДГ исследовали методом просвечивающей электронной микроскопии (электронный микроскоп TESLA BS500), а их химический состав – с помощью электронного сканирующего микроскопа Philips XL30ESEM, оснащенного приставкой локального рентгеновского микроанализа EDS EDAX Pegasus.
Полученные порошки СДГ были использованы в качестве добавки в пластическую смазку Литол-24 (ГОСТ 21150-87) для проведения трибологических испытаний с целью оценки их влияния на трибологические характеристики. Приготовление смазочной композиции осуществляли путем тщательного механического перемешивания при помощи устройства УППС-1. Содержание добавки во всех вариантах полученной смазочной композиции составляло 3 масс. % (оптимальное содержание антифрикционной добавки для универсальных смазок [1]). Для взвешивания использовали аналитические весы ДЛР-200М.
Для оценки трибологических свойств исследуемых смазочных материалов проводили серию лабораторных испытаний на четырёхшариковой машине трения МТУ-1М согласно ГОСТ 9490-75. Испытания каждого образца смазочного материала состояли из серии опытов. При проведении испытаний противоизносные свойства смазочных композиций оценивали по диаметру пятна износа Dи, а антифрикционные – по величине момента трения в контакте деталей пары трения Мт. Каждый опыт проводили на новой пробе испытуемого смазочного материала. Опыты по определению каждого из перечисленных критериев для каждого образца смазочного материала проводили с трёхкратной повторяемостью. Продолжительность работы машины от момента включения до момента выключения электродвигателя при определении показателя износа составляла 1 ч. Испытания проводили под нагрузкой 100 Н.
После остановки машины охлаждали узел трения ниже 40 °С, извлекали шарики и промывали их растворителем. Затем под микроскопом марки БМИ-1 измеряли диаметр пятна износа каждого из трёх нижних шариков во взаимно перпендикулярных направлениях. За диаметр пятна износа Dи принимали среднее арифметическое значение результатов измерений пятен износа девяти нижних шариков трёх последовательных опытов.
Момент трения регистрировали на протяжении всего опыта при помощи тензоизмерительного комплекса (ZET 210, ZET 410, модуль АЦП) и блока PC с установленным программным обеспечением ZETLab. Данный блок регистрировали изменение момента трения каждую 3-ю минуту работы установки. Сравнительному анализу подвергали среднее арифметическое значение результатов всех измерений трёх последовательных опытов.
Результаты исследования их обсуждение
Локальный рентгеновский микроанализ (EDS) показал, что порошки слоистых двойных гидроксидов, полученных при различных соотношениях солей в маточном растворе, могут быть представлены следующими химическими формулами:
1) Zn0,48Cr0,52(OH)2[(NO3))0,24∙0,4H2O;
2) Zn0,64Cr0,36 (OH)2[(NO3))0,18∙0,4H2O;
3) Zn0,72Cr0,28 (OH)2[(NO3))0,14∙0,4H2O.
На рис. 1 представлены электронные фотографии СДГ, полученных при различных соотношениях солей металлов в системе Zn–Cr–NO3. Во всех случаях синтезированные порошки состоят из круглых частиц чешуйчатой формы, имеющих диаметр 20–50 нм.
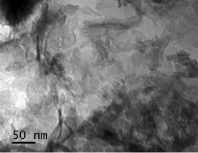
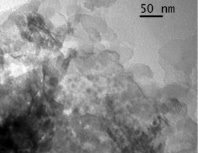
Рис. 1. Электронные фотографии различных порошков СДГ системы Zn-Cr-NO3: Zn:Cr = 1:1 (слева), Zn:Cr = 3:1 (справа)
На рис. 2 приведены кинетические кривые изменения коэффициента трения при испытаниях на четырехшариковой машине для различных составов СДГ исследованной системы. Полученные результаты показывают, что введение в состав стандартной смазочной композиции 3 % добавки СДГ системы Zn–Cr–NO3 при испытаниях способствует снижению равновесного значения момента силы трения примерно на 16 %. При этом величина равновесного значения силы трения устанавливается примерно через 0,5 ч после начала испытаний; в начальный же период испытаний момент силы трения тем меньше, чем выше содержание Zn в составе СДГ (максимальное снижение – при соотношении Zn:Cr = 3:1). Последнее прямо свидетельствует о том, что в первые 30 минут испытаний частицы СДГ играют роль прослойки между поверхностью двух шариков в точках касания; в дальнейшем же, по мере притирания поверхностей и химического модифицирования структуры поверхностного слоя стали, устанавливаются равновесные условия трения.
Следует отметить, что в равновесных условиях трения трибологические характеристики исследованных смазочных композиций зависят от химического состава введенных добавок СДГ (таблица). При увеличении содержания цинка в составе слоистого двойного гидроксида происходит увеличение антифрикционных свойств смазочной композиции. Максимально же увеличение износостойкости (36 %) наблюдается для СДГ, имеющего мольное соотношение Zn:Cr = 2:1. Наблюдаемый эффект можно связать с переходом атомов Cr из состава добавки в состав поверхностного слоя в условиях трибологического контакта.
Рис. 2. Кинетика изменения величины момента силы трения при испытании исследуемых смазочных композиций: 1 – Литол 24; 2 ‒ Литол 24 + СДГ (Zn:Cr = 1:1); 3 – Литол24 + СДГ (Zn:Cr = 2:1); 4 – Литол 24+СДГ(Zn:Cr = 3:1)
Значения трибологических характеристик смазочных композиций на основе смазки Литол-24 (испытания в течение 1 ч) в зависимости от химического состава частиц СДГ
Химический состав антифрикционной добавки |
Трибологические характеристики |
|
Диаметр пятна износа, мм |
Равновесное значение момента силы трения, Н∙м (⋅103) |
|
Без добавки (Литол 24) |
0,64 |
5,83 |
Zn0,48Cr0,52(OH)2[(NO3))0,24∙0,4H2O |
0,46 |
5,01 |
Zn0,64Cr0,36 (OH)2[(NO3))0,18∙0,4H2O |
0,43 |
4,85 |
Zn0,72Cr0,28 (OH)2[(NO3))0,14∙0,4H2O |
0,56 |
4,93 |
Использование добавок СДГ системы Zn–Cr–NO3 обеспечивает снижение значения коэффициента трения, сопоставимое с эффектом, достигнутым ранее для систем Co–Al–CO3, Mg–Al–CO3 и Ni–Al–NO3 (12–17 %); однако при этом обеспечивается значительно более высокое улучшение износостойкости трущихся поверхностей (36 % в сопоставлении с 5–10 % для вышеперечисленных систем [7–9]). При этом на трибологические свойства смазок с добавками нанопорошов СДГ влияет не только тип слоистого двойного гидроксида, но и соотношение [Me2+]/[Me3+] в составе СДГ. Максимальное улучшение трибологических характеристик смазочной композиции на основе универсальной смазки Дитол-24 достигается при использовании СДГ состава [Me2+]/[Me3+] ≈ 2:1, характеризуемого наиболее плотной упаковкой элемент-кислородных октаэдров и расположением в межслойном пространстве только нитрат-ионов параллельно гидроксидным слоям [11, 12].
Выводы
Подтверждена перспективность использования наночастиц слоистых двойных гидроксидов (СДГ) в качестве антифрикционных и противоизносных добавок в смазочных композициях. Показано, что основными факторами, определяющими влияние на трибологические свойства смазочных материалов, является выбор солей металлов для синтеза наночастиц СДГ, а также их соотношение в реакционной смеси. Оптимальные трибологические свойства мгут быть получены при выборе комбинации солей металла, обладающего плакирующими свойствами, и металла, увеличивающего износостойкость стали.
Работа выполнена при поддержке ФЦП «Научные и научно-педагогические кадры инновационной России» на 2009–2013 годы, Соглашения 14.B37.21.1219 и 14.B37.21.1080.
Рецензенты:
Решетов В.А., д.т.н., профессор кафедры физической химии, ФГБОУ НИУ СГУ им. Н.Г. Чернышевского, г. Саратов;
Устинова Т.П., д.т.н., профессор, заведующая кафедрой химической технологии Энгельсского технологического института, ФГБОУ СГТУ, г. Энгельс.
Работа поступила в редакцию 18.09.2013.Библиографическая ссылка
Гороховский А.В., Никитюк Т.В., Третьяченко Е.В., Тычков Ю.Ю., Сафонов В.В., Азаров А.С. ТРИБОЛОГИЧЕСКИЕ СВОЙСТВА ДВОЙНЫХ СЛОИСТЫХ ГИДРОКСИДОВ СИСТЕМЫ Zn–Cr–NO3 // Фундаментальные исследования. 2013. № 10-5. С. 1063-1067;URL: https://fundamental-research.ru/ru/article/view?id=32453 (дата обращения: 12.07.2025).