Одной из центральных проблем использования тяжелых углеводородов в качестве топлива для тепловых горелок и двигателей внутреннего сгорания является смесеобразование. Экономичность рабочего процесса, скорость нарастания давления при сгорании, максимальное давление, дымность и токсичность выпускных газов, а также пусковые свойства дизеля напрямую зависят от распыления, смесеобразования, воспламенения и последующего сгорания топлива.
В ходе процессов, протекающих в камере сгорания двигателя, образуется большое количество газообразных и твёрдых компонентов. При экспериментальном определении температуры пламени в зоне горения по излучению продуктов сгорания, особенно для разреженных пламен, часто наблюдается хемилюминесценция, приводящая к большим погрешностям измерения. Неравновесное распределение энергии по степеням свободы наблюдается при быстропротекающих процессах (например, при взрыве). В этом случае следует говорить о поступательной, вращательной, колебательной и электронной температурах. Попытки оптической регистрации температуры приведут к заниженной оценке термодинамической температуры. Однако эта погрешность становится заметной лишь для разреженных пламен, для обычного пламени, горящего при атмосферном давлении, при соответствующем выборе рабочей области спектра и метода измерения, как правило, можно считать излучение пламени тепловым [3]. При горении топлива источниками теплового излучения являются твердые частицы, например, частицы сажи. Причем основная часть теплового излучения частиц сажи приходится на видимый диапазон длин волн. Это делает возможным оптическую диагностику процессов, происходящих в камере сгорания. При изготовлении топливных распылителей даже небольшие отклонения от паспортных размеров составляющих деталей и узлов приводят к ухудшению качества распыливания. Процесс распыливания-смесеобразования в камере сгорания двигателя скоротечен занимает около миллисекунды, поэтому различить местные неоднородности в топливовоздушном потоке без специальных приборов практически невозможно [2]. Таким образом, разработка метода, позволяющего при проведении эксперимента регистрировать с требуемым пространственно-временным разрешением в реальном масштабе времени параметры факела, представляет значительный научный и практический интерес [7, 9]. Данная работа представляет результат обработки экспериментальных данных по разработанной методике получения количественных характеристик факела струи: корневых углов топливных факелов, их длину, наличие местных сгущений и струек.
Целью данной статьи является представление результатов оптической диагностики дисперсионного состава топливно-воздушного факела по разработанной методике.
При определении температуры пламени, неоднородного по Z (соотношение топлива и окислителя), зависимость температуры Т от Z может быть вычислена теоретически и представляет собой кривую с максимумом, лежащим около значения, равного стехиометрическому. Процессы перемешивания топлива и окислителя представляют собой случайный процесс, следовательно, описываются формулой Гаусса. Таким образом, вероятность того, что в данный момент времени, в данном микрообъеме пламени отношение окислителя и топлива будет равно какому-то значению Z, отличному от среднего значения Z0. Вероятность отклонения концентрации топлива, введенного в однородный воздушный поток в данный момент времени или в данной микро-области пламени от ее среднего значения:
где h = 0,7/σ; σ – среднее квадратичное отклонение величины Z от ее среднего значения Z0. Эта вероятность тем меньше, чем сильнее отличается Z от Z0. Зависимость температуры Т от Z может быть вычислена теоретически и представляет собой кривую с максимумом, лежащим около значения, равного стехиометрическому. Средняя оптическая температура Т определяется из соотношения
При измерении методом оптической пирометрии температуры пламени или участка пламени, обладающих неоднородным или меняющимся со временем температурным полем, мы измерим некую среднюю оптическую температуру [3, 5], которая из-за нелинейной зависимости интенсивности излучения от температуры не будет совпадать со средней массовой, средней арифметической, максимальной температурами пламени.
При измерении яркостной температуры пламени для пламени с неоднородным температурным полем мы измерим среднюю оптическую яркостную. Связь этой температуры со средней истинной температурой определяется известной формулой:
где ελ – испускательная способность для длины волны λ.
Из-за нелинейного характера усреднения, свойственного оптическим методам (независимо от того, происходит ли это усреднение по пространству или но времени), средняя оптическая температура не будет равна истинной, средней температуре пламени, около которой происходит пульсация температуры, и эт различие будет тем больше, чем меньше длина волны. Наряду с неоднородным по пространству температурным полем в пламенах наблюдаются периодические изменения температур во времени, даже когда топливо и окислитель подаются непрерывно. Сам процесс горения сопровождается пульсацией температуры. Средняя оптическая температура находится из соотношения, причем усреднение происходит не по пространству, а по времени:
где τ – период пульсаций, T(t) характеризует изменение температуры со временем, т.е., мы находим температуру такого стационарного пламени, монохроматическая яркость излучения которого равна средней по времени монохроматической яркости, излученной пульсирующим пламенем.
Определяя среднюю оптическую температуру, с помощью высокоскоростного микропирометрического комплекса возможно осуществить более тонкую диагностику с микросекундным временным разрешением. При этом измерение можно считать «мгновенным», т.к. время измерения гораздо меньше наименьшего периода колебаний температуры в пламени. Считать же, что мы измеряем температуру в точке, можно в тех случаях, когда в пределах выделенного нами объема можно пренебречь как монотонными изменениями температуры, так и неоднородностью пламени по соотношению топлива и окислителя. Эти условия для различных пламен удовлетворяются при различных значениях величины выделенного объема и времени измерения.
Экспериментальная установка
Техническим средством системы получения и обработки информации может быть высокоскоростной микропирометрический комплекс измерения температуры и скорости распространения пламен, основными элементами которого являются персональный компьютер и высокоскоростная видеокамера Видео Спринт. Программное обеспечение включает в себя пакет анализа экспериментальных данных Origin 7 и свободно распространяемую программу обработки графических изображений ImageJ [4]. Особенность видеокамеры в том, что она может регистрировать излучение слабой интенсивности за счет усиления в микроканальных пластинах, а быстродействие и многокадровая экспозиция обеспечивается электронным затвором. Для применения видеокамер в качестве высокоскоростных пирометров, необходима их предварительная калибровка. При проведении калибровки видеокамеры была выявлена нелинейность отклика измерительной системы в зависимости от времени экспозиции. Калибровочный стенд представлен на рис. 1.
а б
Рис. 1. а – калибровочный стенд: 1 – оптическая скамья; 2 – эталонная лампа ТРУ1100-2350; 3 – источник тока PSH-2035; 4 – высокоскоростная камера ВидеоСпринт; 5 – монитор; 6 – системный блок; 7 – клавиатура; б – график зависимости яркости пикселей изображения в зависимости от времени экспозиции при постоянной освещенности объектива
Экспериментальное исследование отклика измерительной системы при неизменной освещенности объектива на разных временах экспозиции проводилось с помощью эталонной лампы ТРУ 100-2350 [3]. В зависимости от подаваемого на эталонную лампу ТРУ 100-2350 с источника PSH-2035 тока вольфрамовая нить лампы имеет различную температуру и яркость. Также в зависимости от времени экспозиции двумерное изображение вольфрамовой нити, получаемое видеокамерой, получается разной яркости.
Изображение вольфрамовой нити накала было представлено в шкале серого. Все аппроксимированные по экспериментальным данным кривые являются логарифмическими функциями яркости пикселей в зависимости от времен накопления. При этом погрешность аппроксимации не превышает 2 %.
Так, для светового потока, соответствующего температуре Т = 1700 °С, передаточная функция измерительной системы представляет собой y = a – b·ln(x + c), коэффициенты a = 15,68534 ± 0,3598, b = –5,07267 ± 0,16345, c = 0,38808 ± 0,04772. Поставив в соответствие подаваемый на лампу ток и яркость пикселей изображения, можно ввести новую калибровочную шкалу, связывающую яркость пикселей изображения и температуру регистрируемого видеокамерой на данной экспозиции светящегося объекта. График аппроксимированной функции представлен на рис. 2.
Рис. 2. Аппроксимированная функция соответствияяркости пикселей изображения температуре (погрешность 2 %)
Введенная шкала позволяет использовать данную оптоэлектронную измерительную систему в качестве высокоскоростного микропирометра.
Результаты обработки данныхпо предлагаемой методике
Для апробации методики были использованы шлирен-фотографии топливно-воздушного факела нового форсуночного модуля и факела распыливания для исходного устройства при 3 кПа перепада давления воздуха, взятые из работ [6, 10] и приведенные на рис. 3.
Известно, что при распыливании топлива через сопла форсунки с малыми отверстиями в цилиндре образуется кольцевой факел из мелких частиц топлива. Частицы топлива в виде факела должны заполнять все пространство камеры, однако не достигать стенок поршня цилиндра и сгореть во взвешенном состоянии. При визуальном наблюдении впрыскиваемое топливо должно быть туманообразным, без сплошных струек и легко различимых местных сгущений.
На фотографии нового модуля, подготовленной к градиентному анализу, заметно, что сформированная смесь имеет более мелкодисперсный состав, поэтому обеспечивает полноту сгорания за счет более полного перемешивания в режиме турбулентного наддува. Однако заметна также некоторая асимметрия и оптические неоднородности мантии топливо-воздушной смеси впрыснутого топлива, что говорит о возможности в будущем улучшить данный модуль
Для апробации методов расчёта скорости двухфазной топливно-воздушной струи, приведенных в работах [1, 3], использовался видеофрагмент высокоскоростной видеосъемки процесса распыла топлива форсункой Nissan Atlas, приведенный на рис. 4, б.
Положение фронта струи определялось по переднему максимуму градиента яркости и график его движения показан на рис. 4, а, где по оси Y откладывались координаты точек максимального удаления от точки распыла. Расстояние задано в пикселях. По оси Х – соответствующий момент времени.
Методика позволяет получить также данные о корневых углах топливных факелов и оценить распределение частиц аэрозоля по их длине [8]. Для анализа был взят экспериментальный кадр процесса распыления топлива, полученный в работе [6], выполненный в системе «Видеоскан» VS-SST-285 с экспозицией 39 мкс, время задержки синхроимпульса от датчика давления – 300 мкс. Угол конуса распыла и угла отклонения его оси от оси форсунки характеризуют качество распыла и влияют на процесс смесеобразования и сгорания топлива. Впрыснутое в камеру сгорания топливо должно равномерно заполнить весь объем камеры для хорошего перемешивания с воздухом. Уменьшенный против нормального угол конуса оставляет часть камеры незаполненной топливом, что ухудшает смесеобразование и ведет к недоиспользованию части кислорода воздуха, предназначенного для сгорания топлива. При увеличенном угле распыла часть топлива, попадая на стенки камеры, превращается в нагар и не участвует в образовании смеси. Двигатель при этом снижает мощность, ухудшается его экономичность. Аналогичные явления происходят и в том случае, когда ось конуса распыла отклоняется от оси форсунки (боковой впрыск). По техническим требованиям угол конуса распыла для форсунок большинства дизелей 25°. Ось конуса распыла должна совпадать с осью форсунки.
а б
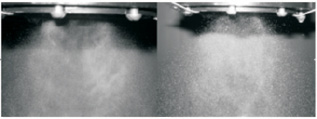
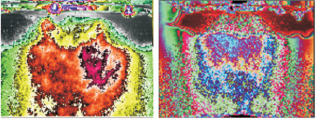
Рис. 3. Фотографии факелов:а – нового форсуночного модуля; б – факела распыливания для исходного устройства при 3 кПа перепада давления воздуха; Обработка изображения топливного факела: Байесовское восстановление «псевдо» цвета оптической плотности; градиент неоднородностей; изолинии плотности; дисперсность и ее градиент; в – новый модуль; г – исходный модуль
Рис. 4. а – график зависимости координаты фронта топливной струи от времени; б – изменение оптической неоднородности исследуемой струи с течением времени; в – гистограммы площадей изотемпературных зон струи
а б в
Рис. 5. а – цифровое фото факела; б – изотемпературные зоны, выделенные на изображении топливной струи; в – гистограмма изотемпературных зон топливной струи
Из анализа топливной струи на рис. 4, б, в видно, что максимальная концентрация топлива наблюдается у распылителя, в начальной зоне струи и во фронте (меньше, чем у распылителя), а также наблюдается отклонение оси керна факела от оси форсунки. Как показывают опыты, изменение угла конуса распыла на 10° и отклонение оси конуса от оси форсунки допустимы на 3–5°.
Причиной изменения указанных величин могут быть отложения твердых частиц нагара в сопловом отверстии и на штифте форсунки, а также износ сопла и штифта.
Выводы
Изучение процесса впрыска при дизельном смесеобразовании требует наличия достоверной информации о связи скоростных характеристик топливной струи с динамикой цикла топливоподачи. Оптические методы исследования не разрушают структуру топливного факела и позволяют получить информацию о структуре и динамике развития факела. Получение данных для обработки с помощью высокоскоростного микропирометрического комплекса может гораздо улучшить качество диагностики. Результат обработки экспериментальных данных по предлагаемой методике согласуется с ранее полученными результатами [6, 10], что говорит о больших перспективах дальнейшего развития данного метода экспресс-диагностики для получения численных характеристик дисперсности топливных струй и повышения экологии процессов горения тяжелых углеводородов.
Рецензенты:
Гуляев П.Ю., д.т.н., заведующий кафедрой ФХПМ Югорского государственного университета, г. Ханты-Мансийск;
Мартынов С.И., д.ф.-м.н., директор Политехнического института Югорского государственного университета, г. Ханты-Мансийск.
Работа поступила в редакцию 19.07.2013.
Библиографическая ссылка
Атюцкая Л.Ю., Бебия А.Г., Бороненко М.П., Серегин А.Е. ОПТИЧЕСКАЯ ДИАГНОСТИКА ДИСПЕРСИОННОГО СОСТАВА ТОПЛИВНО-ВОЗДУШНОГО ФАКЕЛА // Фундаментальные исследования. 2013. № 8-6. С. 1297-1302;URL: https://fundamental-research.ru/ru/article/view?id=32125 (дата обращения: 06.09.2025).