Точность является одним из основных показателей качества изготавливаемой продукции и с точки зрения надежности технологической системы по ГОСТ [1] принимается в качестве основного критерия ее работоспособности.
Точность машинной обработки характеризуется величиной фактической погрешности размеров и формы обработанной детали и зависит от многих факторов, участвующих в процессе ее изготовления. На погрешность обработки детали оказывают влияние все элементы технологической системы. Конечный размер детали можно рассматривать [2] как случайную величину, которая зависит от случайных и систематических погрешностей обработки, тогда общая погрешность примет вид:
Dо = Dсл + Dс. (1)
Случайные погрешности изменяются в пределах как партии деталей, так и в каждой детали в отдельности. Появляются эти погрешности из-за неравномерности припуска на обработку, нестабильности режима резания, ошибки измерений и др.
Систематическая погрешность постоянна в пределах обработки данной партии деталей или изменяется закономерно. Систематические погрешности разделяются на постоянные и закономерно-переменные, тогда полная систематическая погрешность выглядит таким образом:
Dс = Dп + Dзп. (2)
Постоянные погрешности появляются от геометрических погрешностей станка, режущего инструмента и приспособлений, а также от погрешностей размерной настройки станка. Закономерно-переменные погрешности возникают от затупления инструмента, температурных деформаций узлов станка. В течение длительного периода работы причиной появления систематических погрешностей является в первую очередь износ основных формообразующих элементов машины. Преобладающим фактором при обработке партии деталей является затупление инструмента, выражающееся износом резца.
При обработке древесины резанием конечный размер детали определяется фактическим положением плоскости резания. Возникающие при резании силы воспринимаются инструментом и приспособлением, в котором инструмент закреплен, а также деталью и приспособлением, в котором она установлена и закреплена, благодаря чему образуется замкнутая силовая система «станок ‒ приспособление – инструмент – деталь» (СПИД). Упругость системы СПИД приводит к деформациям ее элементов под действием сил резания и закрепления, инерционных и других сил и к образованию погрешностей форм и размеров обрабатываемой детали. Периодическое изменение силы резания обусловливает соответствующее периодическое изменение деформаций системы СПИД, то есть вибрацию. Упругие деформации обусловлены отжатиями основных узлов и отдельных элементов технологической системы, а также контактными деформациями и в общем случае могут достигать 20…40 % от суммарной погрешности обработки.
Непостоянство сил резания в процессе обработки детали, обусловленное изменением сечения срезаемой стружки, изменением механических свойств материала, износом и затуплением режущего инструмента, колебаниями снимаемого припуска материала, различной жесткости детали ввиду неоднородности физико-механических свойств древесины, вызывает и неравномерность упругих деформаций системы СПИД, что влияет на точность обработки заготовки.
Возникает задача оценки вклада в формирование закономерно-переменных погрешностей обработки древесины двух факторов: износа инструмента и деформации системы СПИД, чему и посвещена данная работа.
Материал и методы исследования
Исследования изменения размеров обработанных деталей в зависимости от износа инструмента проводили на действующем предприятии ООО «НИК» в г. Сысерть Свердловской области на четырехстороннем продольно-фрезерном станке С25-4А, со скоростью подачи 14 м/мин, при частоте вращения ножевых головок: нижней ‒ 3043 мин–1, правой и левой ‒ 6076 мин–1, верхней ‒ 5898 мин–1. Обрабатывали пиломатериал с влажностью 12 %, порода сосна, номинальная ширина 115 мм; толщина 30 мм; длина 2 м. Ножи на фрезах были поставлены к началу исследований плоские из инструментальной стали марки 8Х6НФТ: на верхней и нижней ножевой головке упрочненные с использованием концентрированных потоков высокой энергии (пучков ионов азота); на левой и правой – без упрочнения. Во время исследований станок не поднастраивался.
Опытные доски брали из одного места поставок в выборочном порядке. Выборка включала в себя 50 досок без гнили, косослоя, трещин и других недопустимых дефектов.
Станок настраивали на изготовление деталей номинальной толщиной 27 мм, шириной 111 мм. Определение точности обработки производили в соответствии с ГОСТ 7315-92 [3]. Через каждые 30 минут работы станка выбирались по 5 опытных досок, каждый образец измеряли до фрезерования и после фрезерования по ширине и толщине в трех сечениях: посредине и на расстоянии 50 мм от торцов. Измерения проводили с помощью электронного штангенциркуля с ценой деления 0,01 мм. Для каждой выборки определяли среднее значение каждого размера.
Для оценки влияния жесткости системы СПИД на точность обработки заготовок проводились исследования деформаций валов верхней и левой боковой ножевых головок четырехстороннего продольно-фрезерного станка «Beaver 523» в лаборатории кафедры станков и инструментов УГЛТУ. Нагружение валов производилось с помощью настроечных механизмов станка, сила определялась динамометром сжатия ДОСМ-3-1, для измерения деформации использовалась стойка с индикатором часового типа (рис. 1).
Сила прикладывалась к валу в средней части ножевой головки, и в этом же сечении определялась величина деформации (рис. 2).
Измерения проводились при нагружении и разгрузке троекратно и по усредненным значениям строились графики зависимости силы и деформации.
Результаты исследования и их обсуждение
Полученное в результате проведенных исследований изменение размера изделий в процессе обработки показано на рис. 3.
Как видно, с течением времени работы конечный размер детали увеличивается. Увеличение толщины изделия описывается уравнением вида
h = 0,0009t + 26,941 ± D1, (3)
конечный размер по ширине детали, обрабатывавшийся не упрочненными ножами, изменяется более интенсивно, а уравнение для увеличения ширины изделия имеет вид
b = 0,0021t + 111,19 ± D2, (4)
где D1, D2 – суммарная случайная погрешность обработки, соответственно по толщине и по ширине детали.
Учитывая, что в соответствии с нормами точности по ГОСТ [3] отклонения размера при данном виде обработки не должно превышать 0,2 мм, размер детали после фрезерования по толщине выйдет за пределы допуска через 222 минуты (0,2/0,0009 = 222), а по ширине – через 95 минут (0,2/0,0021 = 95).
Рис. 1. Установка приборов для измерения сил и деформаций на верхней (а) и левой боковой (б) ножевых головках четырехстороннего продольно-фрезерного станка «Beaver 523»
Рис. 2. Схема нагружения и измерения деформации валов ножевых головок четырехстороннего продольно-фрезерного станка «Beaver 523»
а б
Рис. 3. Графики зависимости конечных размеров деталей от продолжительности работы инструмента
Результаты исследования зависимости сил и деформаций в системе СПИД представлены на рис. 4.
Как видно нагрузочные и разгрузочные зависимости силы и деформации валов несколько различаются ввиду трения в соединениях деталей и гистерезиса в их материалах. Однако с достаточной для решения поставленной задачи точностью можно принять средние коэффициенты пропорциональности силы и деформации валов ножевых головок: верхней 7589 Н/мм и левой боковой ‒ 40303 Н/мм.
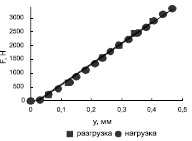
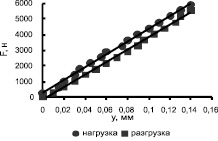
Рис. 4. Графики зависимости силы и деформации валов верхней (а) и левой боковой (б) ножевых головок четырехстороннего продольно-фрезерного станка «Beaver 523»
Из уравнения изогнутой оси двухопорной балки с нагруженной консолью [4]
(5)
можно выразить приведенную к валу постоянного диаметра жесткость сечения EJ:
(6)
где дробь F/y и есть определенный из опыта коэффициент пропорциональности. В таблице указаны значения размеров балок, коэффициентов пропорциональности и приведенной жесткости сечений валов верхней (а) и левой боковой (б) ножевых головок.
Расчет приведенной жесткости валов
Головка |
L, мм |
C, мм |
EJ, Нмм2 |
Верхняя |
230 |
180 |
3,360∙1010 |
Боковая |
230 |
100 |
4,433∙1010 |
Для определения деформации валов в процессе фрезерования выполним расчет сил резания на основе решения обратной задачи [5]. Окружная касательная сила резания средняя за оборот фрезы
(7)
где P – мощность электродвигателя механизма резания, кВт; h – к.п.д. механизма резания; V – скорость резания, м/с.
Средняя сила резания на дуге контакта лезвий с древесиной, исходя из баланса работы сил:
(8)
где D – диаметр фрезы, мм; lк – длина дуги контакта лезвия с древесиной, мм; z – количество лезвий фрезы. Длина дуги контакта лезвия с древесиной
(9)
где t – глубина фрезерования, мм.
Для станка «Beaver 523» с частотой вращения шпинделей 6000 мин–1, диаметром фрез 125 мм, мощностью двигателя верхней головки 11 кВт, двигателя левой головки 5,5 кВт, считая к.п.д. пары подшипников качения 0,99, с количеством лезвий на фрезах 4, глубиной фрезерования 2 мм, получим для ножевых головок: верхней Fхзуб = 1722 Н и левой боковой Fхзуб = 1174 Н. Приближенно, полагая, что мгновенная сила резания нарастает по закону треугольника, можно принять ее максимальное значение равным удвоенному среднему, тогда получим для ножевых головок: верхней Fхmax = 3444 Н и левой боковой Fхзуб = 2348 Н.
Радиальная сила (сила отжима), влияющая на деформацию валов в направлении, нормальном к поверхности обработки в зависимости от касательной силы, определяется по формуле
(10)
где j – среднее значение угла, соответствующее средине угла контакта jк.
. (11)
Исходя из сделанных предположений, максимальная сила отжима составит для ножевых головок: верхней Fхmax = 109 Н и левой боковой Fхmax = 74 Н. Ввиду дорезонансного режима работы валов можно считать их прогибы пропорциональными нагрузке, тогда деформация в средней части лезвия ножа фрезы не превысит 0,014 мм для верхней головки и 0,002 мм ‒ для боковой. Считая кривизну изогнутой оси вала малой, а также ввиду жесткости корпусов ножевых головок, примем, что деформация вала пропорциональна длине участка консоли. Тогда максимальный прогиб на конце верхней ножевой головки вала приближенно составит 0,023 мм, а у левой боковой ‒ 0,003 мм. Эта величина прогибов валов на порядок меньше, чем отклонение размера детали 0,2 мм, обработанной на четырехстороннем продольно-фрезерном станке, допускаемое по нормам точности [3].
Выводы
1. Износ и затупление режущих кромок лезвий инструмента при продольном цилиндрическом фрезеровании вносит систематическую погрешность конечных размеров детали, приводя со временем к их увеличению.
2. Скорость изменения конечного размера детали, обрабатываемой ножами из инструментальной стали марки 8Х6НФТ, упрочненных с использованием концентрированных потоков высокой энергии (пучков ионов азота), в 2,33 раза ниже, чем у не упрочненных ножей этой же марки.
3. Жесткость системы СПИД оказывает влияние на деформации валов ножевых головок фрезерного станка под действием сил отжима.
4. Величина деформаций валов ножевых головок реального фрезерного станка «Beaver 523» на порядок меньше, чем отклонение размера детали допускаемое по нормам точности для четырехсторонних продольно-фрезерных станков.
Рецензенты:
Пашков В.К., д.т.н., профессор кафедры станков и инструментов, ФГБОУ ВПО «Уральский государственный лесотехнический университет» Минобрнауки России, г. Екатеринбург;
Уласовец В.Г., д.т.н., профессор кафедры мехаической обработки древесины ФГБОУ ВПО «Уральский государственный лесотехнический университет» Минобрнауки России, г. Екатеринбург.
Работа поступила в редакцию 07.03.2013.
Библиографическая ссылка
Полякова Т.В., Новоселов В.Г. ВЛИЯНИЕ РАЗЛИЧНЫХ ФАКТОРОВ НА ФОРМИРОВАНИЕ ПОГРЕШНОСТЕЙ ОБРАБОТКИ ДРЕВЕСИНЫ // Фундаментальные исследования. 2013. № 4-4. С. 838-842;URL: https://fundamental-research.ru/ru/article/view?id=31282 (дата обращения: 05.09.2025).