В течение последних 30 лет в сырьевой базе отечественной и мировой нефтехимии ведущая роль принадлежит низшим олефинам – этилену и пропилену. Так, производство этилена в России составляет более 30 млн т/год и постоянно растет [1]. Основным источником их производства служит процесс термического пиролиза углеводородов. Именно на установках пиролиза получают сегодня первичные продукты, обеспечивающие сырьем производство пластических масс, синтетических смол, каучуков и волокон. Но помимо образования основных газообразных продуктов – этилена и пропилена, образуется большое количество побочных продуктов, так называемых жидких продуктов пиролиза (ЖПП). Так, при получении этилена выход ЖПП при пиролизе прямогонного бензина может достигать 20 % [2], а при пиролизе керосино-газойлевых фракций – до 50 % [3], т.е. количество жидких продуктов пиролиза зависит от вида перерабатываемого нефтяного сырья.
Решение проблемы утилизации побочных продуктов производств низших олефинов (этилена и пропилена), получаемых путем пиролиза различного углеводородного сырья, является важной инженерно-экономической задачей при организации эффективного производства.
Состав жидких продуктов пиролиза зависит не только от режима процесса пиролиза, но и от вида используемого сырья – газа, прямогонного бензина, атмосферного газойля. Так, при использовании атмосферного газойля при пиролизе образуется фракция С9 с очень низким содержанием дициклопентадиена (ДЦПД) (около 2 %), в то время как при использовании прямогонного бензина его содержание может достигать 17…20 %. Дициклопентадиен, таким образом, является одним из важнейших компонентов жидких продуктов пиролиза. Полимер, получаемый на его основе, является отличным конструкционным пластиком, однако единственным способом получения изделий из этого вещества является реакционно-инжекционное формование, которое является трудоемким и длительным процессом [9].
Альтернативной технологией получения полидициклопентадиена является его полимеризация в растворе толуола в непрерывном реакторе вытеснения под действием каталитической системы AlEt2Cl:TiCl4.
Непрерывный реактор вытеснения рассматривают как модель идеального вытеснения. Условие идеальности такого аппарата состоит в том, что каждый элемент реакционной массы в данном поперечном сечении движется вдоль оси потока с одинаковой линейной скоростью (поршневой режим). Это предполагает отсутствие торможения потока стенками или насадкой, а также отсутствие диффузионных явлений и продольного перемешивания. При стационарном режиме работы, т.е. при постоянстве скорости подачи и состава исходной смеси, а также условий теплообмена, каждый элемент потока пребывает в таком реакторе в течение одинакового времени, а концентрации и температура в каждом поперечном сечении остаются постоянными. В реакторе идеального вытеснения концентрации веществ изменяются не во времени, а по длине аппарата.
Режим течения, близкий к идеальному вытеснению, имеет место в длинных трубах постоянного поперечного сечения при значениях критерия Рейнольдса, характерных для развитой турбулентности [4]. При этом отношение длины трубы к ее эквивалентному диаметру должно быть больше 20.
Полное математическое описание процесса представляется покомпонентным материальным балансом и тепловым балансом элементарной ячейки dVP для малого промежутка времени dt, т.к. параметры потока меняются по длине аппарата и во времени.
Результаты исследования и их обсуждение
В качестве модели был принят идеальный реактор вытеснения, не отягощенный продольным и обратным перемешиванием, работающий в адиабатическом или изотермическом тепловом режиме. Для такой модели наиболее просто составить математическое описание, которое в общем случае должно включать в себя уравнения материального и теплового балансов, а также граничные условия, налагаемые на модель из практических соображений.
Из ранее проведенных исследований [5–7] известно, что проведение полимеризации дициклопентадиена и сырья, содержащего этот мономер, при температурах свыше 60 °С приводит к получению частично сшитых полимеров, что ухудшает растворимость продукта в ароматических и хлорированных растворителях. Кроме того, при повышенных температурах образуется большое количество коротких полимерных цепей, что приводит к общему снижению молекулярной массы образующихся продуктов, а также к расширению молекулярно-массового распределения. Поэтому одним из ограничений, принятых при моделировании реакционного устройства, является наибольшая достигаемая температура в реакторе, равная 60 °С. В качестве растворителя для проведения полимеризации дициклопентадиена в реакторе вытеснения выбран толуол – вещество инертное как по отношению к мономеру, так и к компонентам каталитической системы – TiCl4 и AlEt2Cl.
Математическое описание реактора включает в себя уравнения материального баланса по мономеру и компонентам каталитической системы, а также уравнения теплового баланса получения полидициклопентадиена [8].
Полученную систему обыкновенных дифференциальных уравнений решали для различных начальных условий (концентрация мономера в толуоле, расход мономера, диаметр реактора).
Рис. 1. Зависимость достигаемой температуры при полимеризации дициклопентадиена под действием каталитической системы AlEt2Cl:TiCl4 (1:1 моль, 2,0 масс. %) от концентрации мономера:1 – 1570, 2 – 1470, 3 – 1370 моль/м3 (адиабатический реактор диаметром 0,1 м, объемный расход раствора мономера в реактор 4,1 м3/ч)
Температура, достигаемая в адиабатическом реакторе вытеснения, определяется концентрацией дициклопентадиена в растворе толуола. Определение концентрации мономера, при которой максимальная температура в реакторе составит 60 °С, является необходимым условием для определения оптимальных значений расхода раствора мономера и диаметра реактора.
Из рис. 1 видно, что оптимальная концентрация мономера в толуоле составляет 1470 моль/м3 (кривая 2). При этом значении в реакторе любого диаметра и с любым объемным расходом мономера температура не превысит максимально допустимую. При больших концентрациях мономера выделяется большее количество тепла, вследствие чего растет температура в реакторе. При меньших концентрациях температура в реакторе ниже, поэтому полимеризация протекает медленнее, а для достижения максимального значения степени превращения требуется большая длина реактора.
Для реакторов с диаметром 0,05; 0,1 и 0,15 м провели анализ степени превращения от объемного расхода (рис. 2). В каждом из реакторов максимальная степень превращения быстрее всего достигается при расходе раствора со скоростью 2,1 м3/ч (кривая 1), однако в реакторе диаметром 0,15 м (рис. 2, в) не соблюдается режим идеального вытеснения, поскольку отношение длины трубы к ее диаметру меньше 20.
а б
в
Рис. 2. Результаты моделирования степени превращения при полимеризации дициклопентадиена при концентрации мономера 1470 моль/м3 под действием каталитической системы AlEt2Cl :TiCl4 (1:1 моль, 2,0 масс. %) при расходе:1 – 2,1; 2 – 4,1; 3 – 6,1; 4 – 8,1; 5 – 10,1 м3/ч, для адиабатического реактора диаметром:а – 0,05; б – 0,1; в – 0,15 м
Оптимальным выбором является реактор диаметром 0,1 м и длиной 3,2 м при объемном расходе раствора мономера в реактор 4,1 м3/ч. В таком реакторе быстро достигается максимальная степень превращения и оптимальная температура (рис. 3), кроме того, такой реактор обладает большей производительностью, по сравнению с реактором, в котором расход раствора мономера составляет 2,1 м3/ч. Кроме того, длина реактора диаметром 0,1 м в несколько раз меньше, чем у реактора диаметром 0,05 м при любом расходе раствора мономера.
Проведение реакции в изотермическом реакторе вытеснения не дает преимуществ по сравнению с адиабатическим реактором, поскольку в изучаемом диапазоне расходов раствора мономера и диаметров реактора скорость процесса остается практически одинаковой как в адиабатическом, так и в изотермическом реакторах (рис. 4). Кроме того, необходимая поверхность теплообмена для изотермического аппарата более чем в 10 раз превышает ее номинальное значение.
При оптимальном расходе раствора мономера в реактор наибольшие различия в скорости протекания процесса наблюдаются для адиабатического и изотермического реакторов меньших диаметров.
Место ввода TiCl4 в адиабатическом реакторе диаметром 0,1 м расположено на расстоянии 0,21 м от впрыска мономера и AlEt2Cl, т.к. максимальная концентрация каталитического комплекса образуется через 1,5 с после начала процесса.
Проведен анализ молекулярной массы полученного полимера и молекулярно-массового распределения, которые находятся в прямой зависимости от скорости образования активных центров, возникающих под действием каталитического комплекса, и достижения системой стационарного состояния.
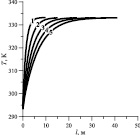
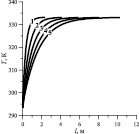
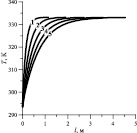
Рис. 3. Результаты моделирования достигаемой температуры при полимеризации дициклопентадиена при концентрации мономера 1470 моль/м3 под действием каталитической системы AlEt2Cl :TiCl4 (1:1 моль, 2,0 масс. %) %) при расходе:1 – 2,1; 2 – 4,1; 3 – 6,1; 4 – 8,1; 5 – 10,1 м3/ч для адиабатического реактора диаметром: а – 0,05; б – 0,1; в – 0,15 м
Рис. 4. Результаты моделирования степени превращения при полимеризации дициклопентадиена при концентрации мономера 1470 моль/м3 под действием каталитической системы AlEt2Cl:TiCl4 (1:1 моль, 2,0 масс. %) при расходе:1 – 2,1; 2 – 4,1; 3 – 6,1; 4 – 8,1; 5 – 10,1 м3/ч, для адиабатического (–) и изотермического (--) реакторов диаметром 0,1 м
Рис. 5. Кинетическая кривая образования первоначальных активных центров в адиабатическом (1) и изотермическом (2) реакторах диаметром 0,1 м, расходе раствора мономера 4,1 м3/ч при полимеризации ДЦПД концентрацией 1470 моль/м3 под действием каталитической системы AlEt2Cl:TiCl4 (1:1 моль, 2,0 масс. %)
Анализ математической модели показал, что в изотермическом реакторе стационарное состояние достигается быстрее, чем в адиабатическом при равных концентрациях мономера и объемном расходе раствора (рис. 5), следовательно, молекулярно-массовое распределение полученного полимера в этом реакторе будет уже, в то время как средняя молекулярная масса полимера в обоих аппаратах будет одинаковой.
Выводы
Предложена математическая модель адиабатического и изотермического реактора полимеризации дициклопентадиена в растворе толуола под влиянием каталитической системы AlEt2Cl:TiCl4 (1:1 моль, 2,0 масс. %).
Смоделированные реакторы для двух тепловых режимов работы при достижении максимальной степени превращения имеют равные геометрические параметры. Оптимальными параметрами аппарата при диаметре 0,1 м и длине 3,2 м являются расход раствора 4,1 м3/ч и концентрация мономера 1470 моль/м3, при которых достигается максимальная степень превращения.
При концентрации мономера 1470 моль/м3 экономически выгоднее использовать адиабатический полимеризатор, т.к. необходимая поверхность теплообмена для изотермического аппарата более чем в 10 раз превышает ее номинальное значение.
Работа выполнена в рамках государственного задания «Наука» по теме 3.2702.2011.
Рецензенты:
Ивашкина Е.Н., д.х.н., доцент кафедры химической технологии топлива и химической кибернетики, ФГБОУ ВПО «Национальный исследовательский Томский политехнический университет», г. Томск;
Короткова Е.И., д.х.н., профессор кафедры физической и аналитической химии, заместитель директора по научной работе и инновационному развитию института природных ресурсов, ФГБОУ ВПО «Национальный исследовательский Томский политехнический университет», г. Томск.
Работа поступила в редакцию 01.07.2013.
Библиографическая ссылка
Ляпков А.А., Бондалетов В.Г., Борисов Г.В. МАТЕМАТИЧЕСКОЕ МОДЕЛИРОВАНИЕ РЕАКТОРА ДЛЯ ПРОВЕДЕНИЯ РАСТВОРНОЙ ПОЛИМЕРИЗАЦИИ ДИЦИКЛОПЕНТАДИЕНА // Фундаментальные исследования. 2013. № 8-3. С. 655-659;URL: https://fundamental-research.ru/ru/article/view?id=31976 (дата обращения: 30.06.2025).